Developing a dry room for an advanced lithium-ion battery production lab is a precise task requiring ultra-low dew point levels. The task becomes monumental when that lab project also included the renovation of an existing space, isolating it from the rest of an occupied building and placing needed mechanical equipment two floors above. Working together, teams from Scientific Climate Systems (SCS), Munters and Innovative Air Systems designed and developed a world-class lab, ensuring consistent and accurate conditions were met. The assignment was undertaken at the University of Michigan Energy Institute’s Battery Lab in Ann Arbor, Michigan. The facility offers state-of-the-art equipment for university researchers, materials scientists and engineers, and suppliers and manufacturers, to develop less expensive and longer-lasting energy-storage devices for grid storage, transportation and consumer products. “Our primary focus in the dry room is electrolyte filling and final cell assembly for lithium-ion batteries,” said Greg Less, Ph.D., senior laboratory manager with the University of Michigan Energy Institute. “A moisture-free environment is essential for longevity and safety in lithium-ion batteries.” Houston-based SCS, specializing in designing and installing precise low-humidity environmental conditions for dry rooms, with more than 200 installations worldwide, was selected to design and build the dry room. The work encompassed a complete integration, mechanical systems, controls for monitoring and adapting to ambient conditions and all the needed equipment to achieve design requirements.
Hızlı bilgiler
- Complete supply and installation of a dry room
- Consistent and accurate conditions optimized for battery production
- Ultra-low dew point of less than 0.5% relative humidity
- Cutting edge mechanical design including Green PowerPurge system for increased energy efficiencies
Lab design challenges
Developing the 700-square foot lab presented several unique challenges. For one, the project required converting an existing, second story space in a three-story building into a dry room. “The building functions as a multi-purpose research and study facility, and the laboratory was to be installed in a space that was used for study work areas,” said David Parkman, senior project engineer with SCS. “Installing this lab meant totally isolating the area from the surrounding adjacent spaces and hallway.” Another challenge was that the mechanical equipment had to be located on the roof and connected to the second floor of the building without disturbing occupants on the third floor.
Strict lab design requirements
The equipment also had to be specified to fit on the available roof space and designed to operate with minimal sound and visual impact. Lab design took more than a year, with several meetings to review design concepts and details to the installation schedule and coordination with a local contractor to arrange roof space and use of an industrial crane to lift the mechanical equipment in place. Based on the size and activity within the room, design conditions were set at 70°F and ≤ -40°C dew point or ≤ 0.5% relative humidity. Maintaining these conditions was essential as high energy lithium-ion batteries must be produced in environments with less than one percent relative humidity to prevent hydrolysis of the electrolyte salt. Lab staff also wanted windows in the dry room for natural light. With the separation of mechanical equipment on the roof and the dry room two levels below, the supply air conditions from the dehumidification system must be maintained to provide the drying capacity needed to control the space at 70°F, ≤ -40°C dew point or ≤ 0.5% relative humidity. “We had to accommodate the needs of the lab but also work around other areas between the mechanical equipment location and the dry room site,” said Parkman. “Therefore, the supply air ductwork needed to be equally vapor tight, and also the return air. “We have to maintain a lab, that’s surrounded by rooms maintained at 75°F with 60% relative humidity, at a half of percent relative humidity,” added Parkman. “That differential makes the integrity of that dry room critical, and we had to ensure every seam was precisely sealed.” SCS ensures all project elements are carried out In other functional areas of the building, multiple small access hatches were required in the dry room to adjust utilities associated with these rooms and other labs. These had to be gasket sealed, along with the room enclosure, to maintain conditions. “Because this space wasn’t meant to be a dry room, let alone a lab, there were several panels needed inside of the room to allow access to control valves and shut-off switches for building services that had to be incorporated into the design,” said Less. SCS utilized its extensive experience to incorporate quality insulated panels and sealed all joints to provide a vapor tight enclosure. All penetrations for sprinklers, electrical power and compressed air were sealed with the same quality control as the room. Lab staff can access the dry room by entering and exiting through an airlock to prevent moisture infiltration from outside. With proper sealing, the dry room requires only 200 CFM of positive pressure to avoid moisture infiltration that would affect conditions inside. To achieve this level of control required a large amount of mechanical equipment, including an advanced dehumidification system, all strategically placed on the building’s rooftop. Munters dehumidification system delivers The design criteria and expected activity within a dry room determine equipment performance requirements. For the University of Michigan Battery Lab, the supply air temperature and moisture needed to be lower than the design set point to accommodate the internal sensible and latent loads from the number of people working in the space, any exhaust air from workstations, and the heat load from people, processing equipment and lights. “The Munters Green PowerPurge desiccant system was chosen as the central component of the mechanical system because it’s specifically designed to meet the needs of advanced battery manufacturers requiring low dew point control, while still consuming less energy than other systems,” said Jeff Siemasko, Munters director of sales, North America. “The Green PowerPurge high performance desiccant system uses the least amount of energy possible, and was developed for the low dew point application required by the lithium-ion battery dry room industry,” said Curtis Musall, president of Innovative Air Systems and SCS OEM account manager for Munters. The Green PowerPurge is energy-efficient because the unit acts as an energy recovery system, collecting waste heat off of the hottest section of the desiccant wheel and using it to help with regeneration. This process reduces the energy required for reactivation, while lowering the discharge temperature of the process air, decreasing energy costs for post cooling air being delivered to the dry room. Lab conditions exceeded expectations “Green PowerPurge can easily supply dew points of -70°F/-56°C supply air while saving between 25% and 45% of the dry room cooling cost and 35% to 50% of desiccant reactivation energy cost,” said Musall. The Munters dehumidification system effectively and efficiently controls the dew point, and the unit’s refrigeration provides the initial stage of temperature and moisture removal before final drying via the dehumidifier for the supply air to the dry room. According to Less, conditions in the facility have actually exceeded expectations. “Our humidity is usually lower than the spec by quite a bit,” said Less. “We are easily able to monitor conditions via a digital readout outside the room that is also connected into the University building monitoring system.” “The support provided by Curtis and the Munters team in confirming the design features and performance was essential to project success,” said Parkman. “Munters has been providing energy-efficient dehumidification systems for this application for nearly 40 years and has been our source for these dry room design specifications.” “Munters quality and performance are consistent with our requirements in designing the facility to control these extreme conditions,” added Parkman. “Where the installation requires total integration, Munters supplied the dehumidification system and Innovative Air Systems provided the refrigeration equipment needed to match the dry room/dehumidification system requirements.” “Scientific Climate Systems worked with us to make sure we received the exact type of lab that we wanted and made sure we understood all of the parameters,” said Less. “Working together we developed a fantastic, world-class space for our customers to produce batteries.” Project Quick Facts Design - 70°Fdb, ≤ -40°C dew point or ≤ 0.5% relative humidity People – Five (5) maximum in the dry room Personnel Entry/Exit – 5 per hour Exhaust – 1000 CFM Panel Enclosure (fire retardant) – 4” walls and ceiling with Unistrut mounting system Personnel Access – Airlock 6’ x 8’ Access Hatches – Nine (9) 24” x 24” gasketed hatches to access building utilities Emergency Exit – Fire rated door sealed to University fire rate hallway walls Penetrations and Sealing for Automatic Fire Suppression Systems heads Floor – Vapor barrier seal and ESD epoxy final finish Windows – Eight (8) triple pane viewing windows in line with building windows Dehumidification - Munters IDS-4500 GPP with gas reactivation, DX refrigeration cooling coils, HEPA filtration and electric post heat Additional Features – Heated snow and mist louvers for winter Controller (Munters) – Siemens Integrated control system with HMI display Dry Room Controller – nCompass controller/HMI with graphical display of room temperature and dew point Room Sensors – Vaisala DMT 342 temperature and dew point sensor Ductwork – Welded seam supply and return ducts with 2” insulation from roof mounted dehumidification system above building 4th floor down to 2nd floor dry room DX Condensing Units – One (1) 25 HP and One (1) 15 HP
Hızlı bilgiler
- Complete supply and installation of a dry room
- Consistent and accurate conditions optimized for battery production
- Ultra-low dew point of less than 0.5% relative humidity
- Cutting edge mechanical design including Green PowerPurge system for increased energy efficiencies
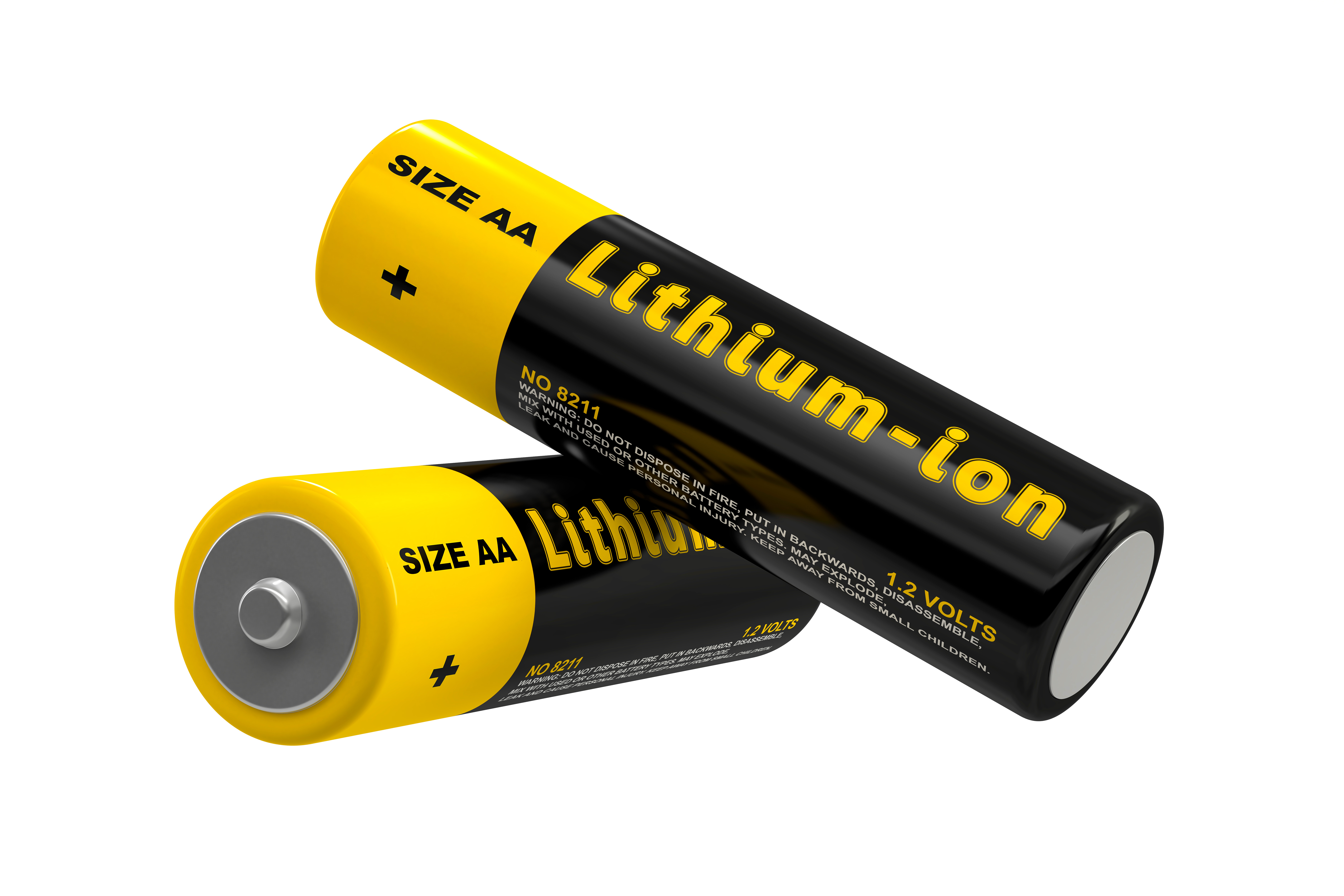
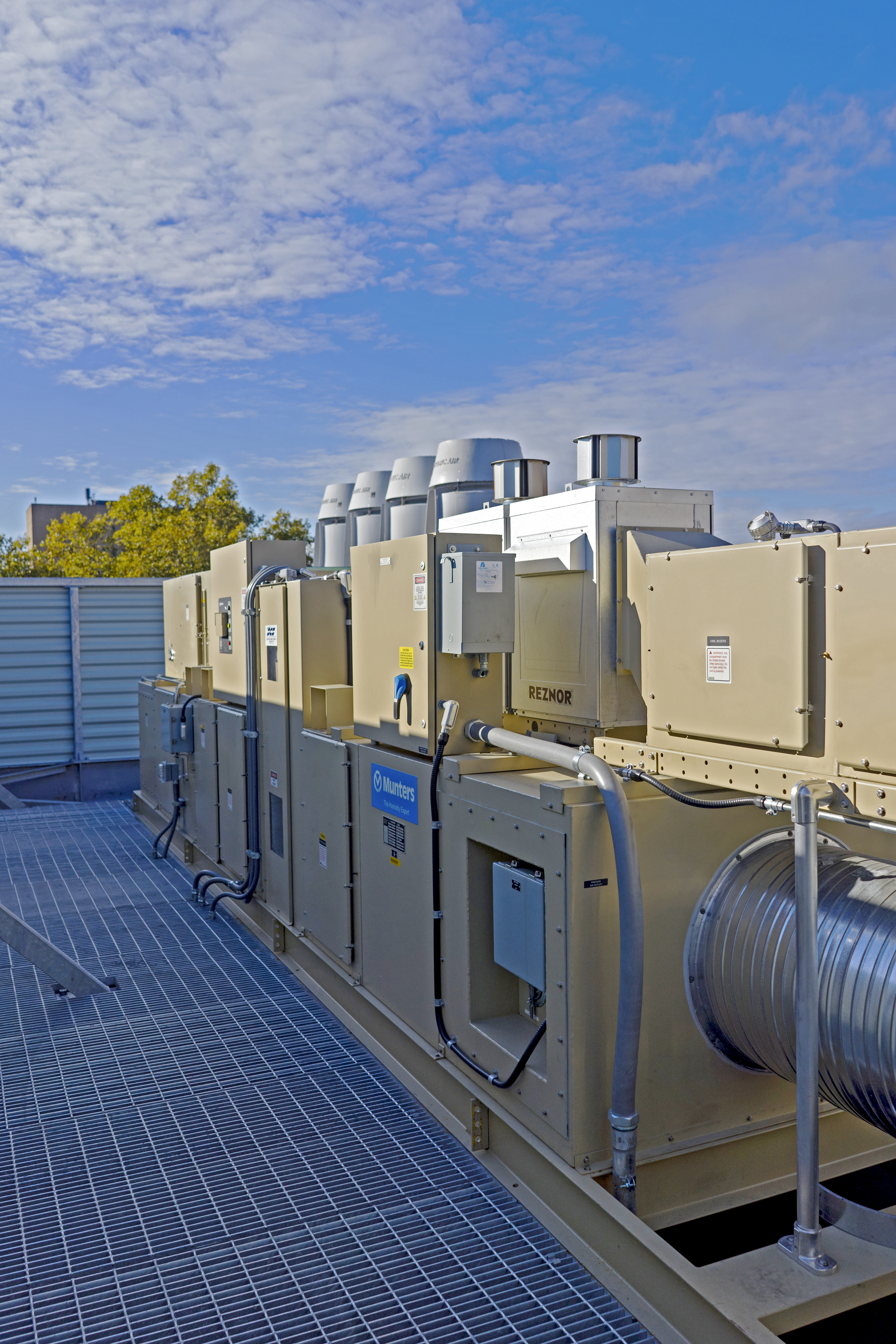