Launched in July 1843, Brunel’s SS Great Britain was the world’s first iron hulled, screw propeller-driven, steam-powered passenger liner. The largest ship of her day, she is the only surviving example of the type. She was returned as a hulk to Bristol in 1970 and over the past 4 years has undergone a massive £11.3 million conservation programme.
Snelle feiten
- Stabilise Corrosion
- Cost Effective
- CFC Free
- Environmentally Friendly
By controlling humidity, Munters creates optimal conditions for products during manufacture and storage. As with SS Great Britain, items are preserved from the corrosive effects of the air’s moisture content. Munters has proven consistent success in meeting the preservation demands of valuable artifacts at: the British Museum, British Film Institute, Hampton Court Palace, and the National Maritime Museum to name a few. Work on this part of the project started on site last year and was completed in time for the ‘re-launch’ celebrations this July. Full information on Brunel’s ss Great Britain and the preservation project is available on the web site www.ssgreatbritain.org. If you are looking for a solution or improvement through humidity control, make Munters your call. How It Works - The Munters Principle All Munters’ sorption dehumidifiers are equipped with drying wheels, called rotors. The rotor contains small air ducts with a very large contact surface and is treated with a substance, such as silica gel, that easily absorbs moisture. The running and maintenance of the dehumidifier is very cost effective and CFC-free and so is environmentally friendly.
A unique design to preserve the 1840’s iron hulled ship, to stop deterioration of the ship’s hull in its dry dock, was required. The 100m long iron hull is surrounded at waterline level by a glass plate covered by a thin layer of water, which forms the ‘roof’ of the massive dehumidified chamber. Munters were approached by WSP Consulting Engineers to assist in their design of the conservation system for SS Great Britain which would dehumidify the lower hull below the glass plate and the inside of the ship itself to provide a controlled dry environment and stabilise the corrosion of the iron. Munters also worked in conjunction with regional construction company Bluestone and Building Services contractor MJN Colston. Capita Symons was the project and cost manager and Space Decks built the glass plate structure, which is providing a massive ‘wow’ factor for the visitors.
Two air handling units were installed – one in the dry dock and one inside the boiler room. A 100 tonne crane was used to lower the dry dock unit into place and the air handling unit in the boiler room was delivered to dockside in individual components. These parts were lifted onto the deck and carried the length of the ship. They were then lowered through the hatch and carried into the boiler room. This process alone took 2 weeks using up to 9 men at any one time. Some of these components weighed up to 1 tonne. Once constructed there was less than 100 mm space left between the air handling unit and the boiler room bulkhead. It was constructed and painted in the boiler room itself. This process took 4 weeks to complete. Both units were specially designed and incorporate Munters dehumidification rotors. Each unit is approximately 8 metres long and 3 metres high and weighs 8 tonnes. The dry dock unit has 7 double glazed viewing panels to allow visitors to see the inside of the unit working.
Snelle feiten
- Stabilise Corrosion
- Cost Effective
- CFC Free
- Environmentally Friendly
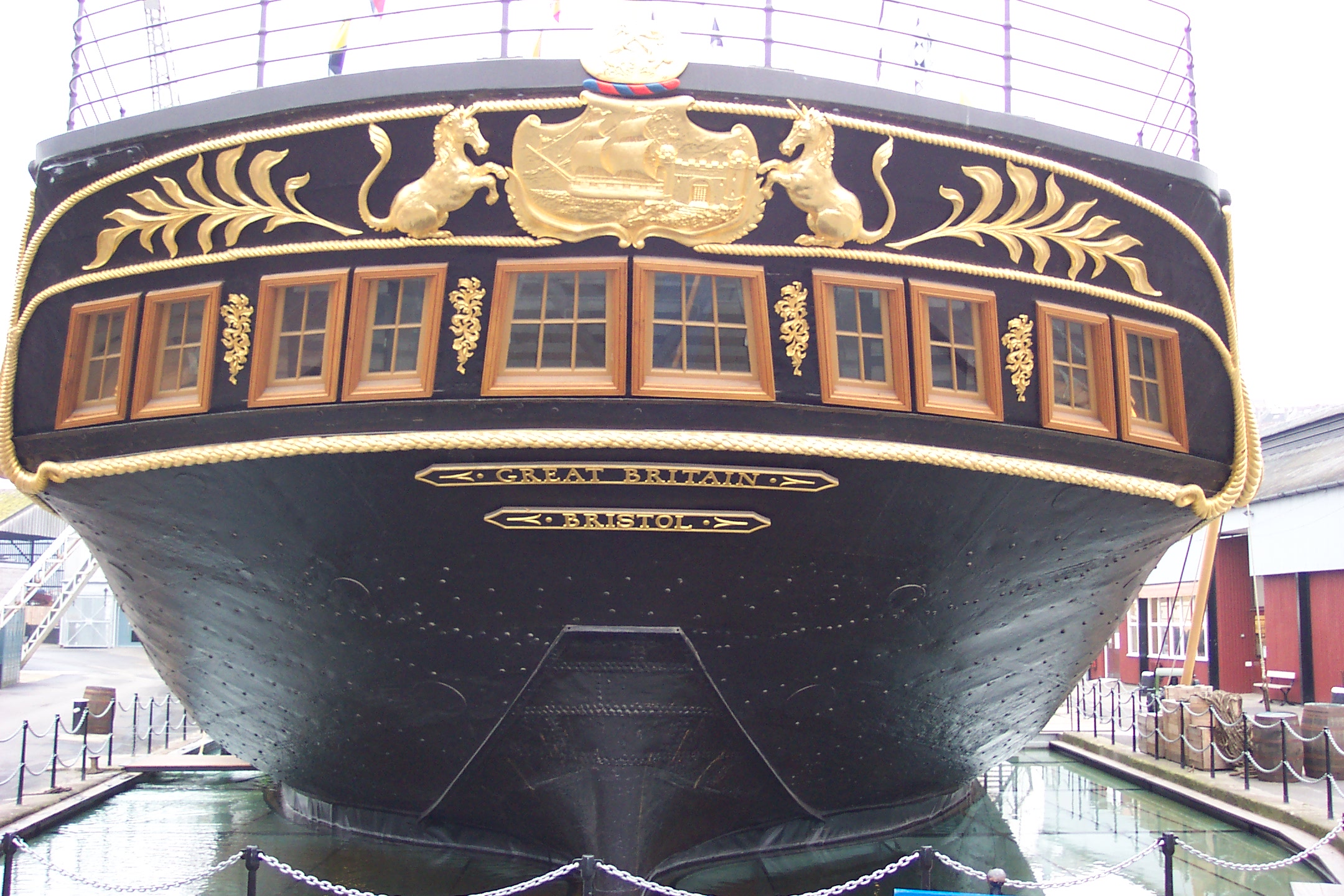
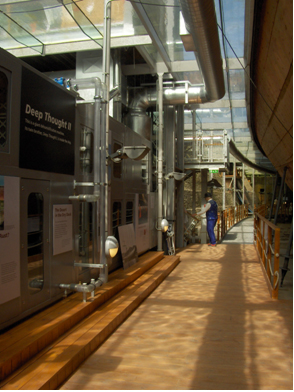
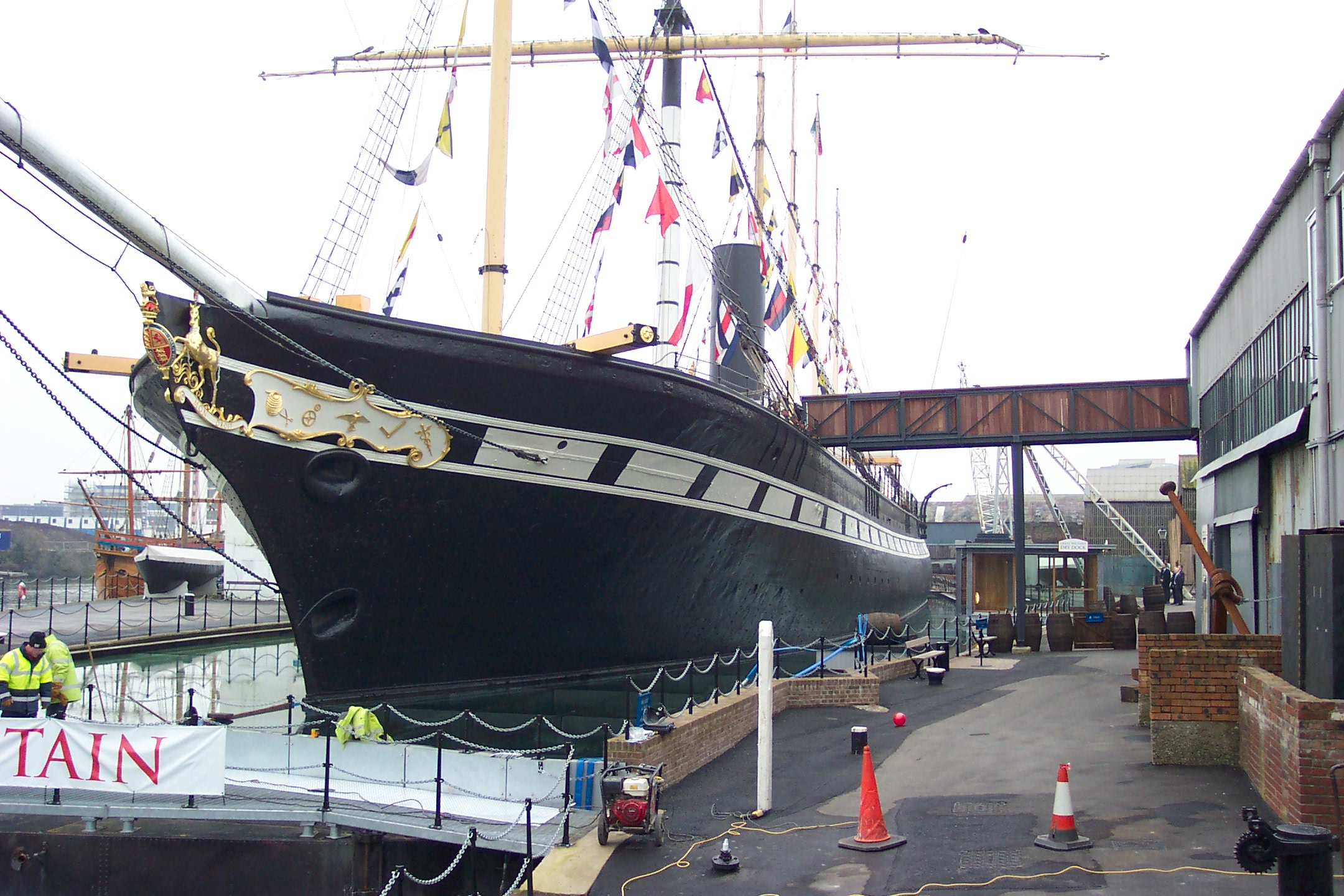