Over 20 years ago, a Canadian coffee producer installed a thermal oxidizer (TO) on their coffee roasters. The oxidizer was installed to address odor concerns from neighboring citizens.
주요 특징
- Reduce energy usage/operating costs
- Cleanable design to provide low maintenance and long equipment life
- Three-year ROI
The 2,000 standard cubic feet per minute (SCFM) oxidizer was sized for three roasters, two at 800 SCFM and one at 400 SCFM. As the oxidizer was approaching its end of life, the customer began looking for an energy saving, cost reducing solution that offered increased capacity for a future additional roasting line. To achieve energy savings, reduce costs and increase capacity, InProHeat Industries, a local oxidizer OEM, was employed to replace the existing thermal oxidizer over a Recuperative Oxidizer (RO) that included an integral Munters Thermo-Z plate type heat exchanger. The new RO was designed with excess capacity to handle the installation of a future fourth roaster for a total of 3,600 SCFM capacity. The Munters heat exchanger was designed to incorporate access doors and wide air channels to facilitate cleaning of the odorous, effluent stream. This customization was important to the customer because of concerns over build-up of tar and chaff (dried skin from the coffee beans), both by-products of the roasting process.
Oxidizer comparison
Compared to the original thermal oxidizer, the addition of the Munters Thermo-Z heat exchanger in the replacement RO has enabled the customer to reduce odor removal costs by 55%, providing 1.5MMBh in energy savings. The roasters are on-line 12 hours per day and the customer is able to achieve well over $30,000/year savings in natural gas costs. The customer projects the addition of the heat exchanger will pay for the heat exchanger equipment and installation costs in just over three years. The customer is currently considering retrofitting Munters Thermo-Z plate heat exchangers in other plants with existing thermal oxidizers. A TO can heat up the coffee roasting effluent stream from 205°F to an oxidation temperature of 1300°F. The 1300°F is then directly exhausted outdoors and is a waste of much valuable energy. The RO uses 1300°F exhaust to preheat roaster effluent from 205°F to 558°F, then send the effluent to the oxidizer. The exhaust air temperature is effectively reduced from 1300°F to 700°F.
주요 특징
- Reduce energy usage/operating costs
- Cleanable design to provide low maintenance and long equipment life
- Three-year ROI
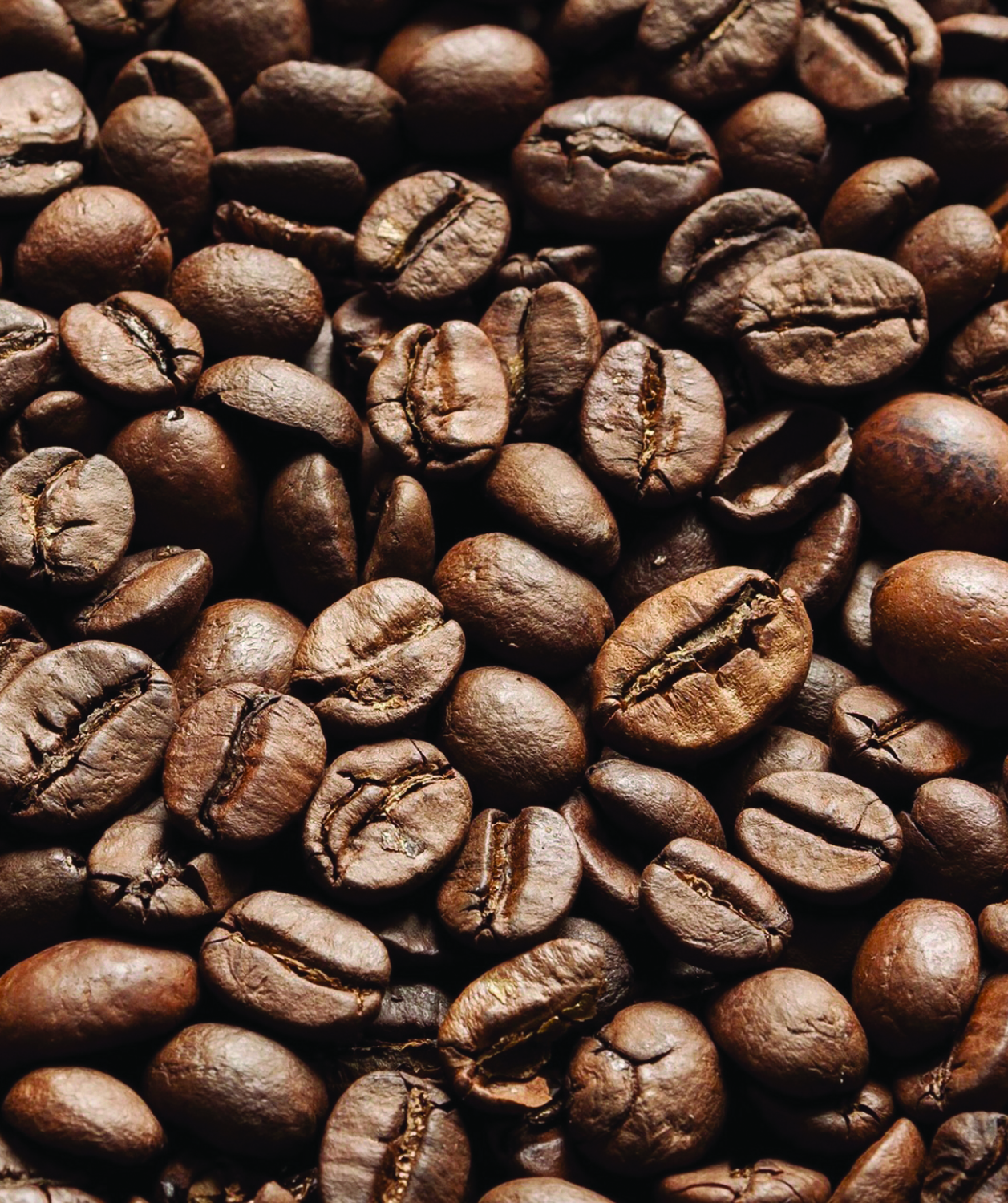
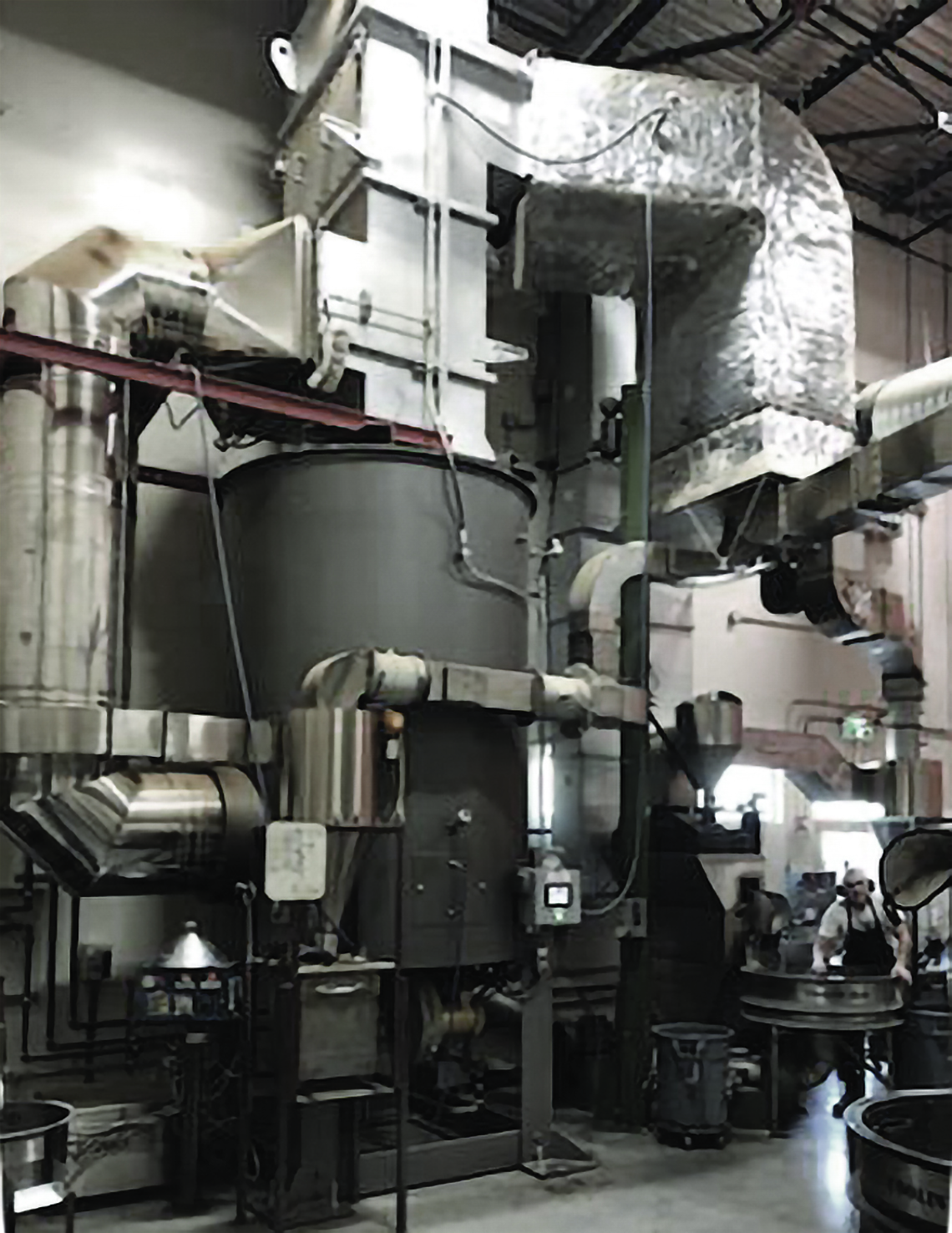