Nestec, Inc. provided two 46,000 standard cubic feet per minute (SCFM) Regenerative Thermal Oxidizer (RTO) systems to a potato processing facility in Idaho. The RTO’s were designed to control emissions from the potato frying portion of processing to meet local air regulations.
주요 특징
- Recover energy to use for another process
- Eliminate unnecessary energy spending
- Reduce plant make-up air requirements
- Reduce noise
Prior to the frying process, the potatoes must move through a number of steps to produce the quality and flavors desired in the final products. The potato drying section of the process, which is the step before frying, requires clean, indirectly heated air to remove about 15% of the moisture in the potato after they have been blanched. The waste energy from the RTO’s could provide a suitable heat source to the dryer when coupled with an energy recovery unit (heat exchanger). Nestec, Inc. approached Munters to design secondary heat recovery systems to preheat the clean air required for the dryers using the waste gas from the RTO’s.
Heat recovery
The cost and availability of energy is a major concern when processing potato fries. The energy demand for a dryer can be reduced by approximately 30% with a properly installed heat recovery system. Air-to-air heat recovery is a major step in achieving the desired end product, and the air that is used in the dryer is a combination of recirculated air and fresh air from the atmosphere. Air that is brought in from the atmosphere passes through an air-to-air heat exchanger where the RTO exhaust air preheats the incoming fresh air. The air-to-air heat recovery is a unique design where the two air streams never see each other or mix, eliminating the possibility of cross contamination between the two air streams. A significant advantage to incorporating a heat recovery system into the process is that the heat recovery unit and fans are located outside the building. This allows the dryer to no longer be dependent upon make-up air sourced from inside the building. In addition, the noise level is greatly reduced when locating the exhaust and make-up fans outside. The air-to-air heat recovery system has a 100% payback in less than a year and guarantees make-up air is filtered, which greatly reduces the energy demand for the dryer. Munters provided four fully insulated heat recovery exchangers. The benefits to recovering the energy have been reduced fuel consumption using the 92,000 SCFM of waste gas at 230°F to pre-heat 68,000 SCFM of clean filtered ambient air, to as high as 190°F (on an average day of 60°F), resulting in over 9,500,000 BTU/hr of recovered energy. “The heat recovery system has been running continuously for many years and has allowed us to successfully recover significant amounts of energy and eliminate unnecessary energy costs,” commented Jim Nester, President, Nestec Inc.
주요 특징
- Recover energy to use for another process
- Eliminate unnecessary energy spending
- Reduce plant make-up air requirements
- Reduce noise
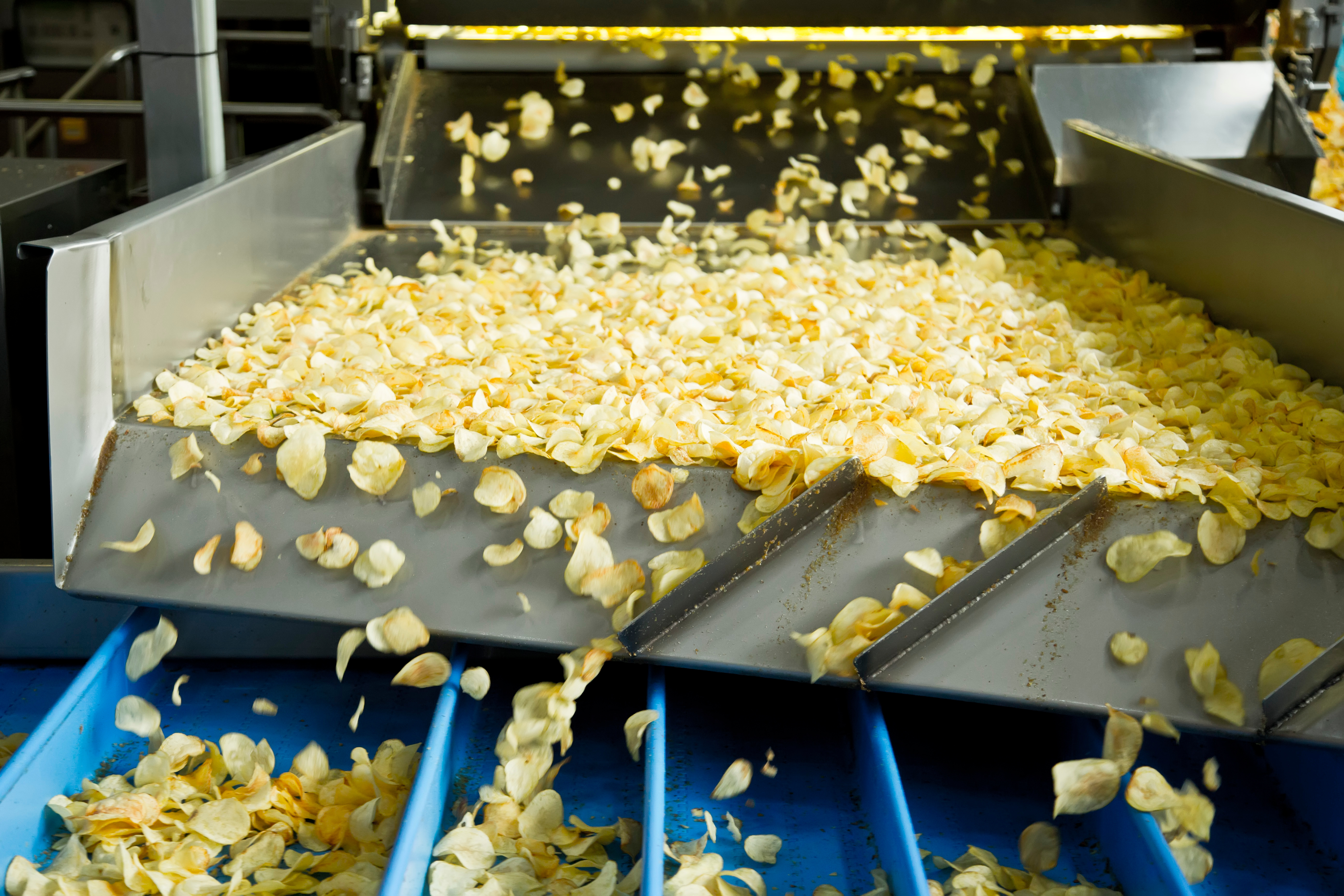
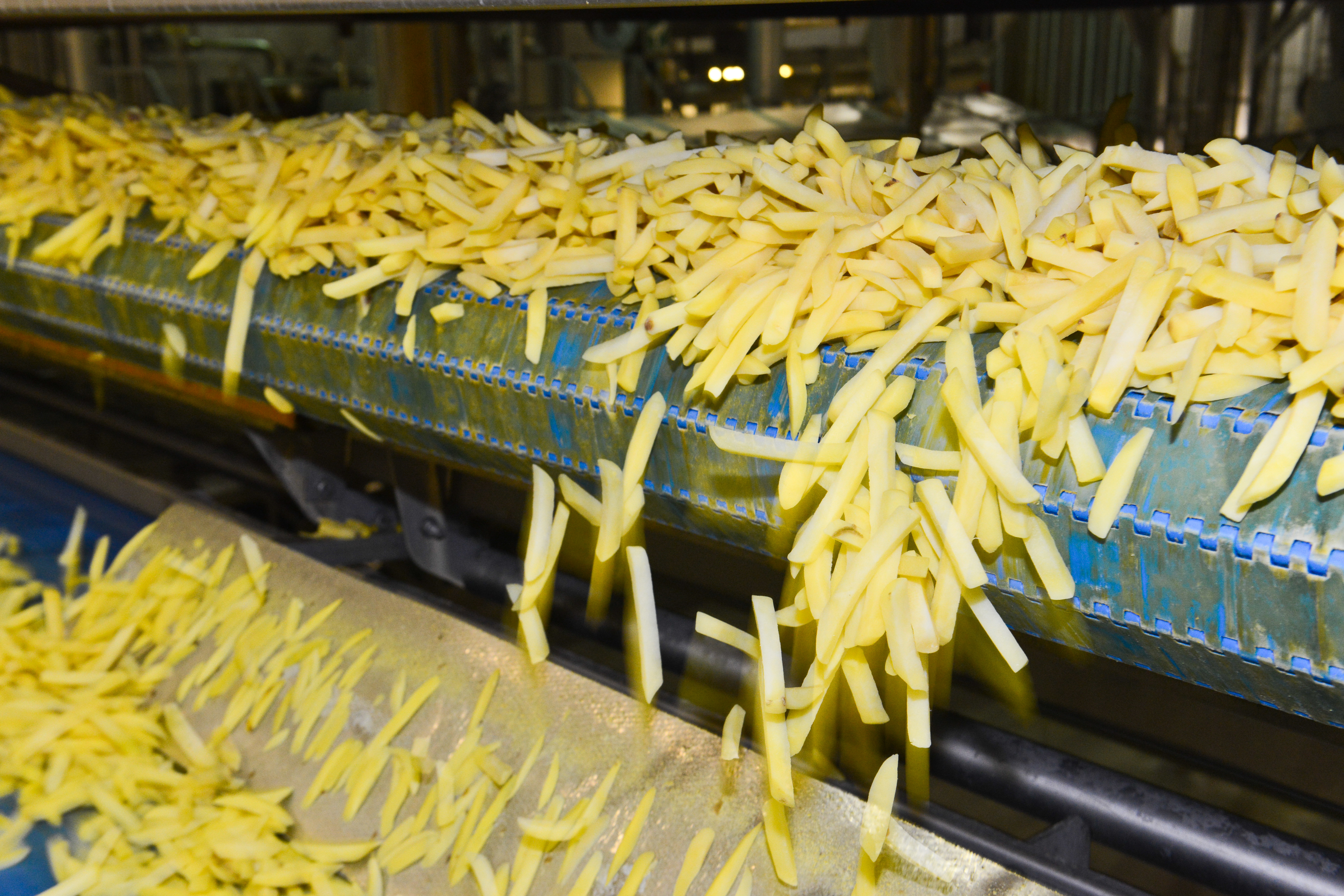
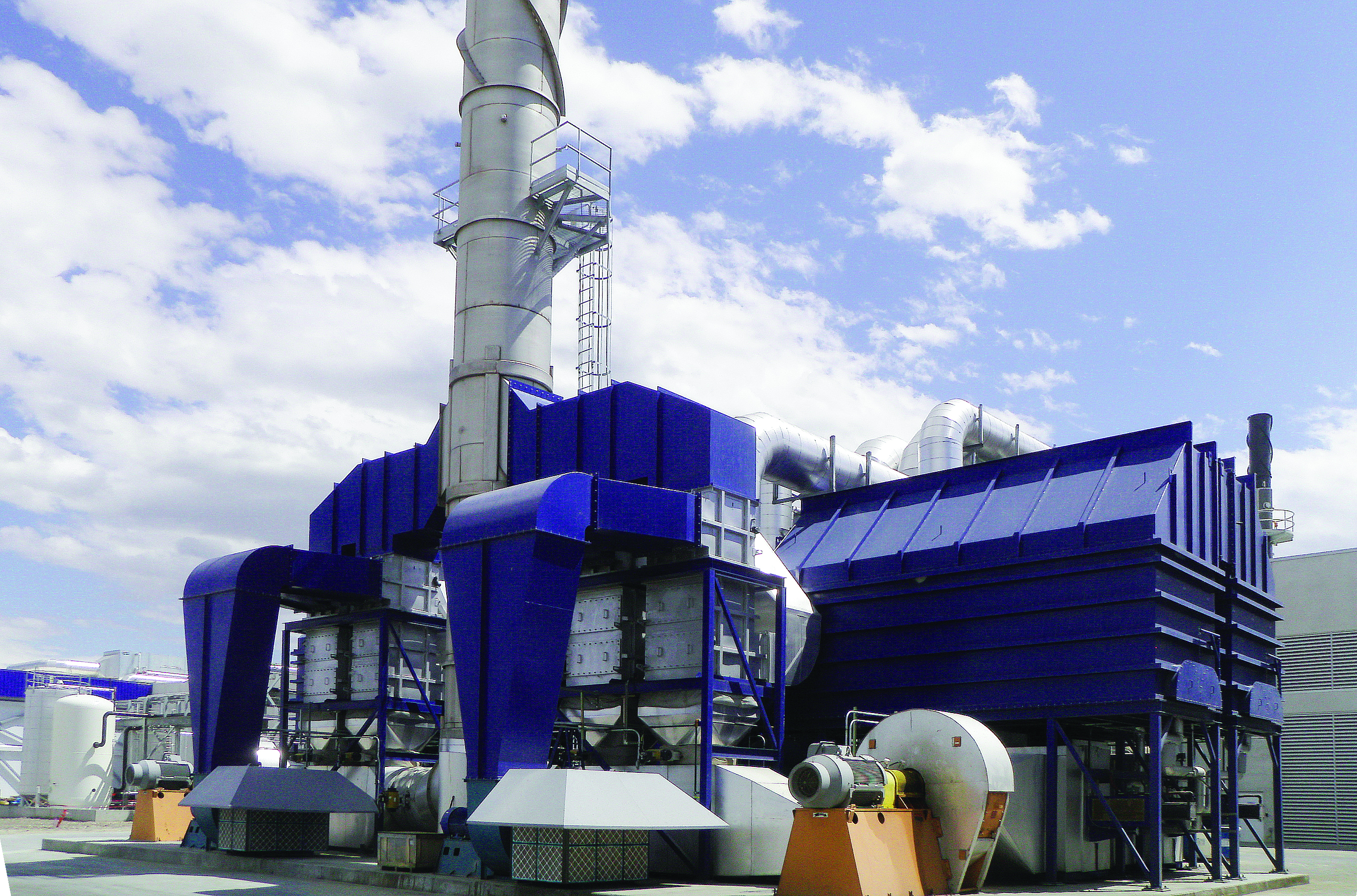