The Essarts poultry plant in France has resolved its problem of frost, condensation and water droplets by drying the air, as the presence of water in the atmosphere creates favorable conditions for bacterial growth and causes discomfort for operators working in cold conditions. The Arrivé group’s Essarts plant, with a 650-strong workforce and processing 450,000 birds per week, has taken an important step through the acquisition of six Munters dehumidifiers, to resolve their humidity problems.
特徴
- Prevents condensation
- Combats frost formation
- Increases workers visibility
- Reduces defrosts
- Improves hygiene
In the wing processing room which is 1,200m3 and kept at temperatures between 4 and 6 °C, the cleaning team are given 2 hours and 30 minutes to do their job. Before, the fifteen technicians’ visibility was limited to 50 cm due to the fog formed by the water jets working at medium pressure. “We installed a dehumidifier, supplying 2,000m3 per hour in a plant of 50,000m3,” says Oliver Bourhis, Factory Manager. “Since then the visibility has been increased to 15 metres! We also wanted to prevent water droplets forming on the ceiling, following advice from the health authorities.”
Drying the air
The dehumidifier has enabled droplets to be absorbed at ceiling level as well as liberating 10-15% of the energy capacity of the cooling equipment working in cold conditions. This has allowed the temperature of the work room to be lowered from 8 °C to 6 °C. The cold store (18,000 m3, at -25 °C) houses a dehumidifier treating an area of 1,400 m3/hr, in an air-treatment plant of 22,000 m3. The aim was to deal with the frost. Essart confirms, “The dryers sublimate the ice. The result is no more frost!” A small dehumidifier is also situated at the air-locked door to the static deep-freeze tunnels (at -30 °C) in order to limit the amount of water droplets created there. This happens due to the difference in temperature, and this also leads to frost formation on the floor caused by the falling droplets. The dehumidifier solves these problems. Another can be found at the dispatch quay for frozen goods. A dehumidifier is also used to limit the frost in the spiral deep-freeze tunnel. Halting production in order to defrost and clean are less frequent, now taking place every 21 hours instead of every 8 hours. The dehumidifier also translates into an increase in returns on materials and energy. With no frost to contend with, the energy exchanges are better which results in the tunnel running more quickly. “We wanted a simple technical solution, which would work well with our refrigerating system and be energy-efficient,” says Bourhis. “We visited the sites of two other companies in our field, who had already installed Munters equipment. They had completely solved their frost problems in the cold rooms and eliminated water droplets on the ceiling of the carving rooms. That made our minds up for us, we did the same thing and it was a success.”
特徴
- Prevents condensation
- Combats frost formation
- Increases workers visibility
- Reduces defrosts
- Improves hygiene
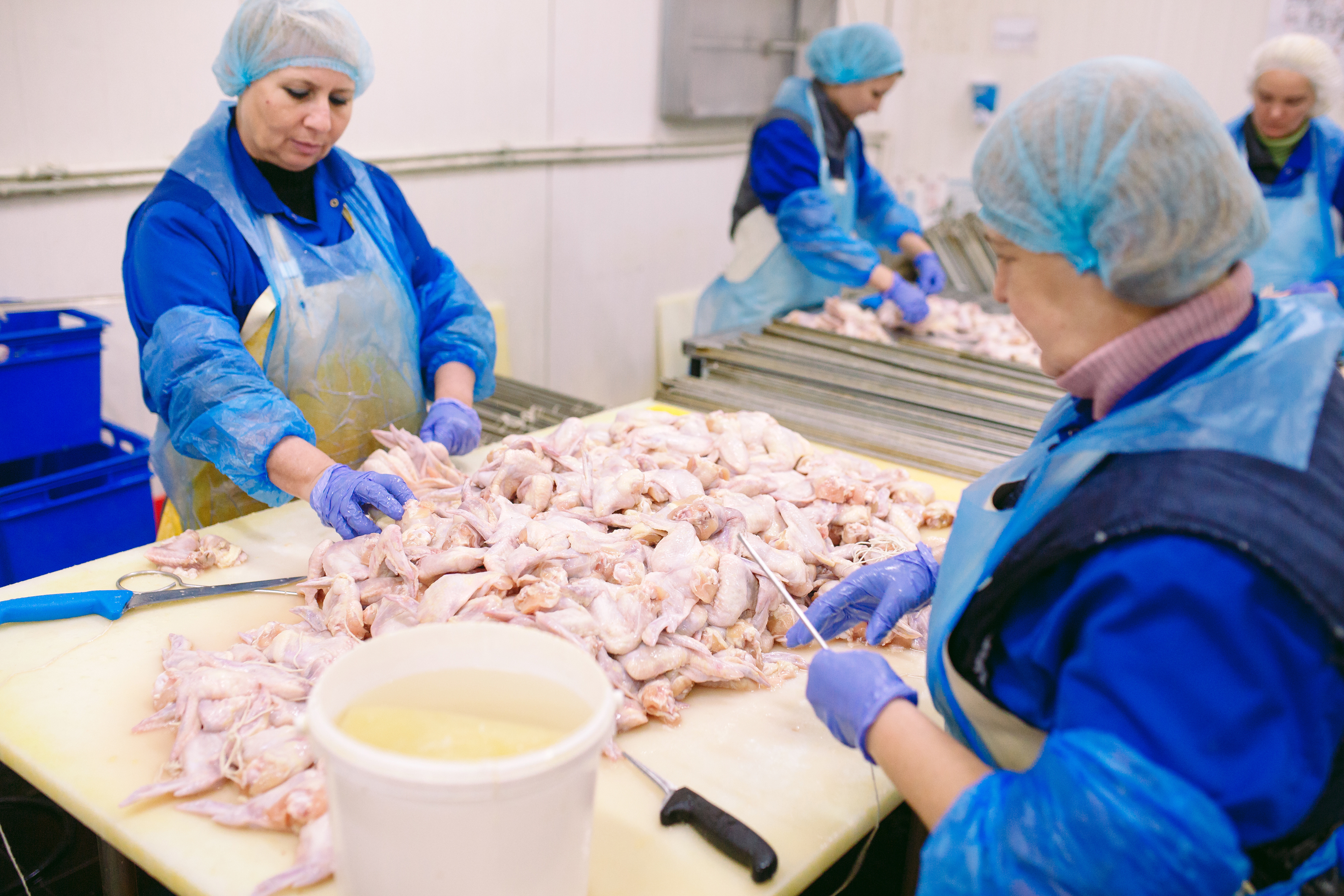
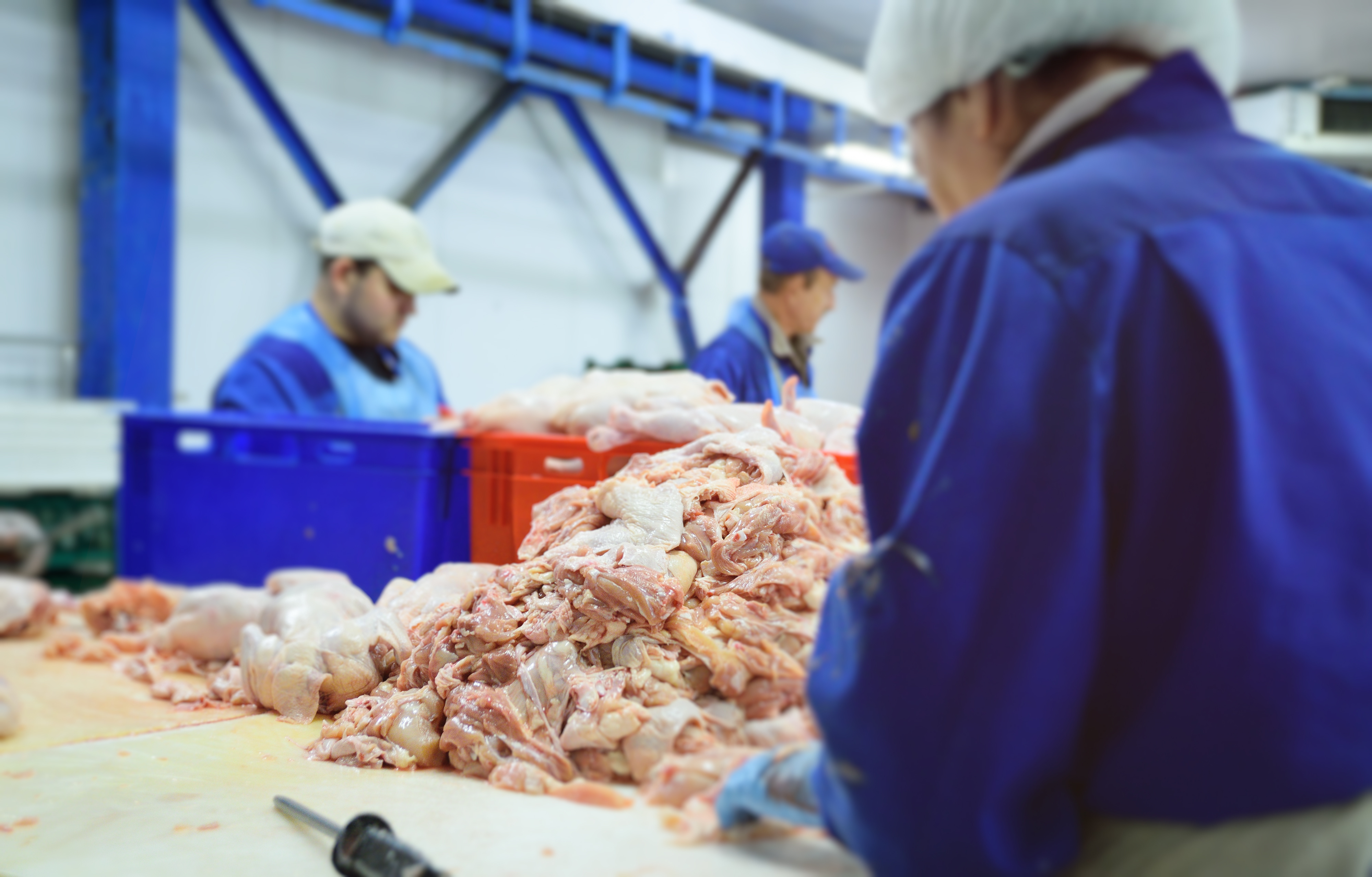
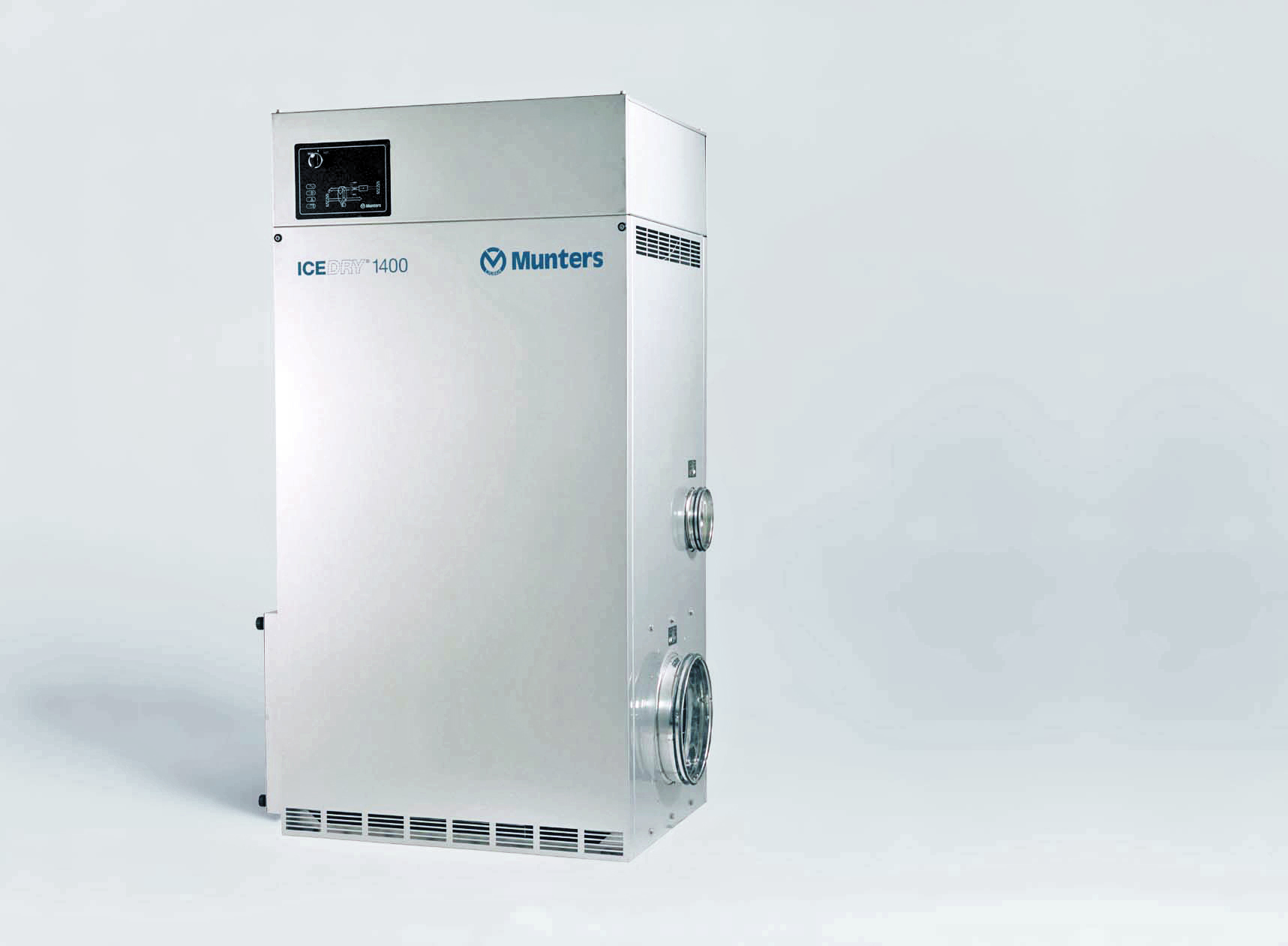