Founded in 1935 in Springdale, Arkansas, Tyson Foods is the world’s largest processor and marketer of chicken, beef, and pork products. Tyson produces a wide variety of protein-based and prepared food products for customers throughout the United States and more than 100 countries. It´s the recognized market leader in its retail and food service markets.
Informazioni rapide
- Condensation eliminated
- Significant energy savings
- Reduced labor costs
The Problem
Two hundred thousand birds are processed every day at Tyson’s Nashville, Arkansas plant. Production staff at the plant were spending a significant amount of time removing condensation that was forming on overhead pipes and ceilings in the evisceration area near the bird chiller. All condensation needed to be removed after sanitation and prior to processing. “We were hanging plastic over our chiller every day. The difference in air temperature was causing the ceiling to sweat,” says Mike Hanson, Complex Manager at Tyson Foods. “We employed two people per shift to mop condensation around the chiller area.” Fans were added to increase airflow in the evisceration area to try and eliminate condensation. This often brings in humid air, adding moisture and creating airflow imbalances that can increase condensation formation. Condensation may also be found in other areas of the plant as a result of changing airflow patterns. Munters was contacted to design and manufacture a condensation control system that would eliminate overhead condensation in this area.
The solution
Louvers and fans were added in several locations, which changed airflow patterns throughout the processing area. An airflow test and balance was conducted to determine the existing airflow patterns, and what actions were required to achieve proper airflow. Air should flow from processing to evisceration and be exhausted from the pick scald area. After analyzing the test and balance report, a 22,000 CFM system with ammonia cooling and desiccant dehumidification was selected. The system was equipped with PowerPurge, Munters patented energy recovery system. A 35% energy savings was recorded with PowerPurge, when compared to a conventional desiccant system. Condensation began to disappear within hours of starting the Munters system. “Since installing the dehumidification equipment, we have not had to hang plastic or have the usual two people per shift to control condensation. We don´t need to dry the ceilings in the morning following sanitation,” says Hanson. “So far we are very pleased with the results and will use this technology in the future to help eliminate condensation.” Hanson is now looking at other areas within the Nashville plant where dry air can help with moisture-related problems.
Informazioni rapide
- Condensation eliminated
- Significant energy savings
- Reduced labor costs
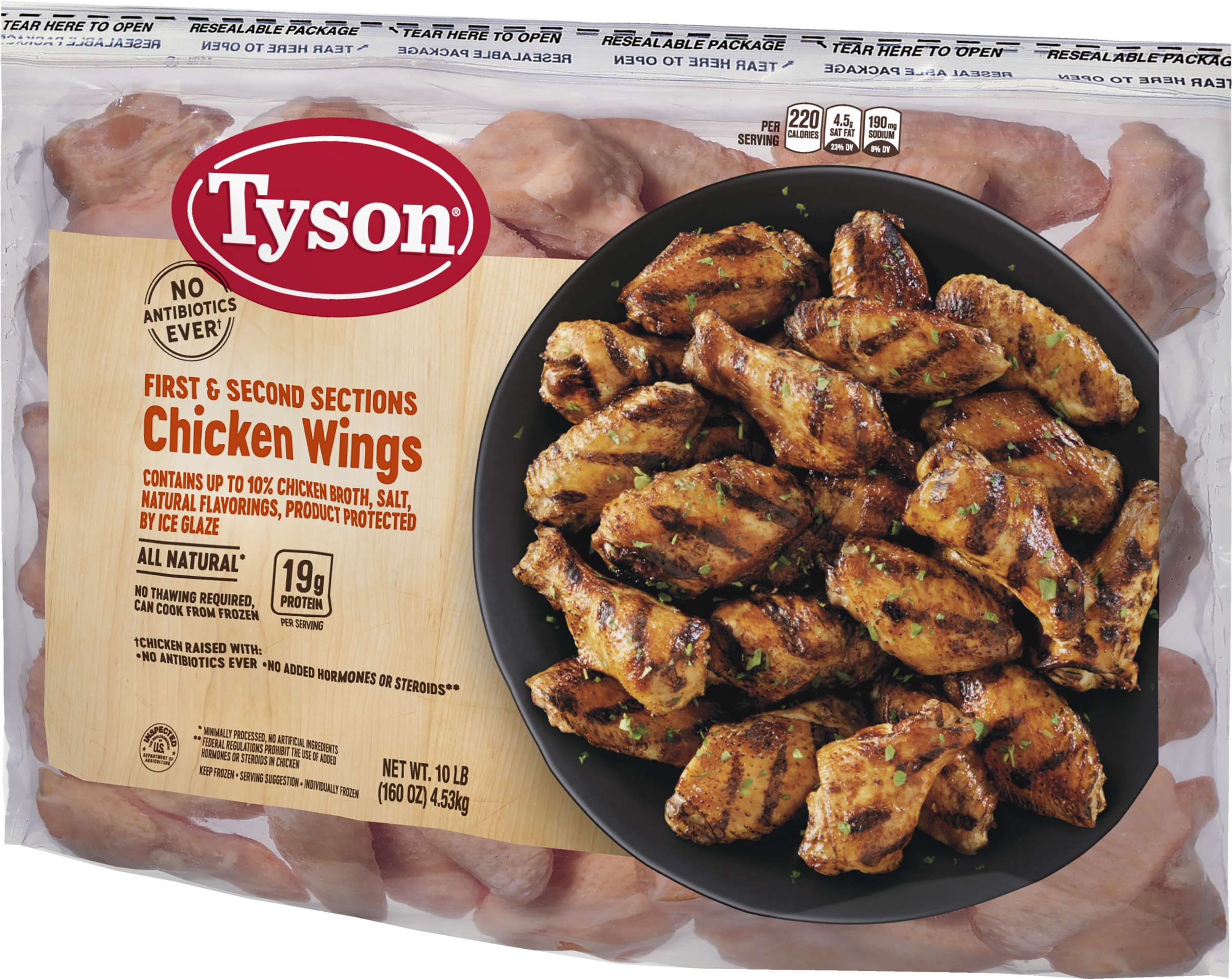
