Laing O’Rourke, Munters and Faber Maunsell have completed a main cable de-humidification system on the centre spans of the Severn Suspension Bridge for the UK Highways Agency, making it the first operational main cable de-humidification system in the UK.
Faits rapides
- Stable conditions
- Prevent condensation
- Extend bridge life
- Stop corrosion
- Constent monitoring
- Increased operational safety
The project involved wrapping the Severn Bridge main cable in polymer based material to create a homogenous seal and to install a de-humidification plant room within the bridge. The plant then drives dry air into the main cable to reduce the level of humidity in it and suspend corrosion of the cable strands. A polymer based material was spirally wound onto the main cable and heat shrunk into position creating a seal between each spirally wound section and a tight fit onto the main cable itself. The sealing system was proof tested on an air test rig with excellent results. With the majority of the work at height above and alongside the busy M48 motorway, twin access cradles were supplied that spanned either side of the main cable. Munters dehumidification system is designed to provide reliable 24/7 operation and real time monitoring. For injection of dry air into the cable the external wire wrapping was removed from around the main cable in three locations on both centre span main cables. Wedges were inserted into the cable strands to open up a path for air flow, 16 Zinc wedges were installed in pairs around the main cable at each location. These stainless steel sleeves were fabricated to a high standard to form a chamber around each of the locations where the main cable had been wedged open and provided an interface connection for the air flow pipework. Air flow was provided from the plant room through the bridge structure and attached to the hanger cables up to the injection points in HDPE pipework, electro-fusion jointed and installed by Laing O’Rourke. The plant room and dehumidification system was designed and commissioned by Munters. The plant room is inside the actual structure of the bridge and all the components, including the dehumidifier, had to be manufactured in sections to enable them to be lowered through the hatch, and then built inside the actual bridge. There were 72 separate sections which required six Munters Service and operations personnel to transport these sections to the site within the bridge and it took a three man team from Munters 5 days to construct the plant room complete with dehumidification system. The bridge is a historic listed building and the necessary approval had to be sought to enable several holes to be drilled into the structure in order for the necessary ductwork to be installed for the dehumidification system. Munters desiccant dehumidifier has monitoring equipment linked to it which records the relative humidity, temperature and air pressure going into the cables. It also records the relative humidity, temperature and velocity of the air coming out of the cables. This ensures that the dehumidification system is working to its optimum capacity. The system has been designed to control the conditions at 20% relative humidity in the plant room, which is then blown up the cable, via the large fans within the plant room. Munters dehumidification system incorporates the moisture absorbing desiccant wheel at the heart of the dehumidifier. Air to be dehumidified in the cables is drawn into the plant room and then through the desiccant dehumidifier, where moisture is absorbed onto the drying wheel and the resulting dry air is delivered back into the cables. Simultaneously a separate air flow is passed through the regeneration sector to remove the absorbed moisture and discharge it to the atmosphere.
Faits rapides
- Stable conditions
- Prevent condensation
- Extend bridge life
- Stop corrosion
- Constent monitoring
- Increased operational safety
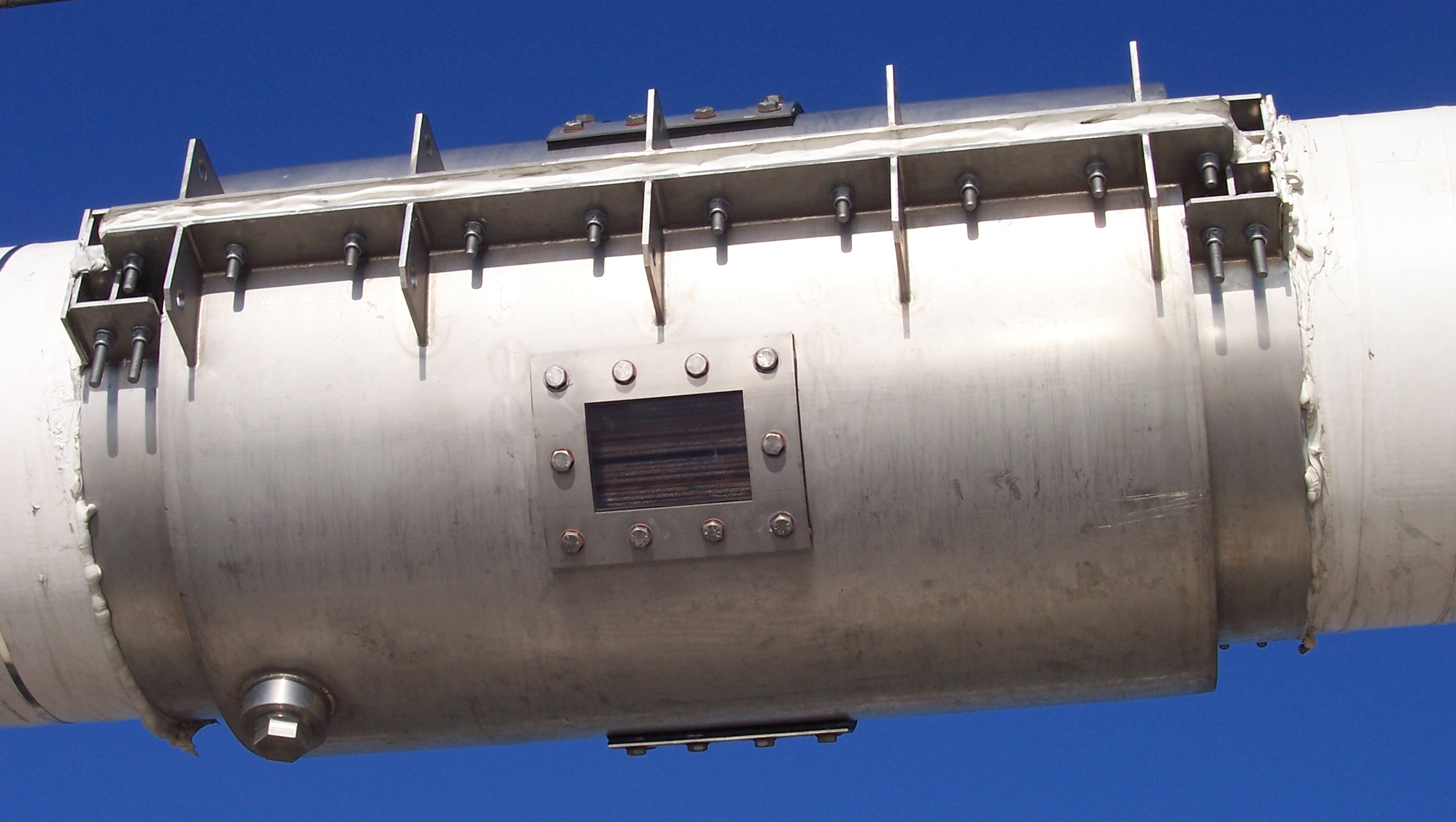
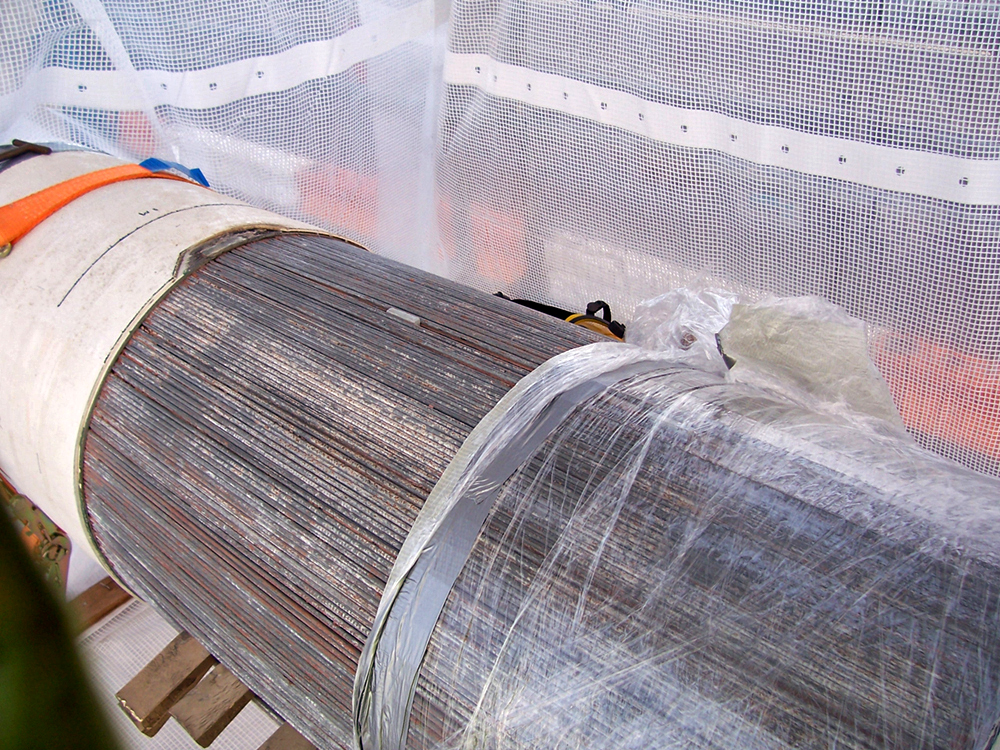
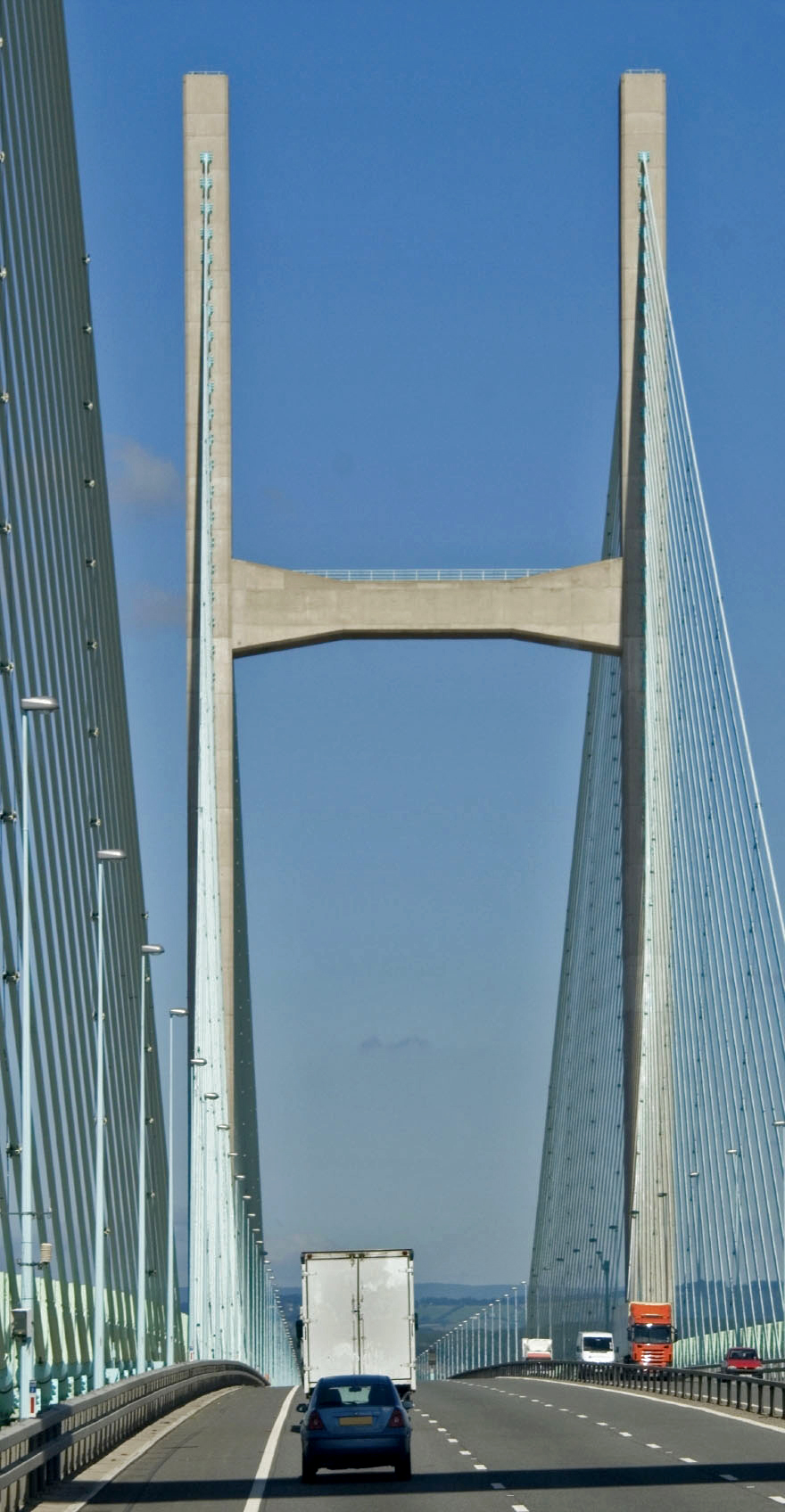