India’s largest producer of formic acic, acetic acid and methanol asked Munters to solve a problem they were having with dislodging trays during start-up of their synthesis gas scrubber. Munters not only solved the problem, but also improved column performance.
Faits rapides
- Customer: Fertilizer Company
- Location: Western India
- Tower Name: Syngas Scrubber
- Tower Diameter: 3048 mm
- Mass Transfer Equipment: Tower Trays (Sieve Trays)
Background
The client operates an integrated ammonia urea complex and is India’s largest producer of formic acid, acetic acid and methanol. It has the world’s largest single stream, fuel oil based ammonia urea plant using Texaco Partial Oxidation of Fuel Oil Process for production of synthesis gas (syngas). Overview The Texaco Gasification Process converts organic materials into syngas, which is a mixture of hydrogen and carbon monoxide. The feed reacts with a limited amount of oxygen (partial oxidation) in a refractory-lined reactor at temperatures between 12000°C (21632°F) and 15000°C (27032°F), and at pressures above 18 atm. The syngas scrubber is used to wash gases coming out of the fuel oil gasifier. The hot gases coming out of the quencher are cooled to 2500°C (4532°F) by cold water and are then fed into the scrubber. The gases are scrubbed in a tray column that has four trays for soot and condensate removal. After scrubbing, the gases are sent to the process section. Customer requirements Operation dislodging of trays was occurring during start-up, which is why the customer asked Munters to study the system and resolve the problem. Problem analysis Munters studied the system and tray construction and the following observations were noted: - The main design constraint of the column trays was the extremely high uplift pressure of 6 bars at start-up, which lasted for about 15 minutes - Gases were infiltrating the trays, and the impingement force was greatest on the lower tray Possible reasons for failure - The direction of the major beam was found to be perpendicular to the flow. It should have been parallel to the flow. The parallel direction of the beam distributes and maintains uniform upward force across the tray deck. - The existing tray clamping method and the bolting pitch was found to be inadequate in overcoming the initial upward thrust, thus dislodging trays - Additional arrangement of sure cleats was not provided Solutions provided After studying the system and checking the mechanical design calculations Munters suggested placing an impingement strip over each row of sieve trays to further facilitate the soot removal. New trays with additional features such as sure cleats, stiffener angles on the tray integral beam and lock nuts for clamping assembly and impingement strips were mechanically designed, manufactured, supplied and installed. Results achieved The dislodgement problem was permanently solved and column performance improved as a result of lower soot carryover.
Applications dans ce cas
Faits rapides
- Customer: Fertilizer Company
- Location: Western India
- Tower Name: Syngas Scrubber
- Tower Diameter: 3048 mm
- Mass Transfer Equipment: Tower Trays (Sieve Trays)
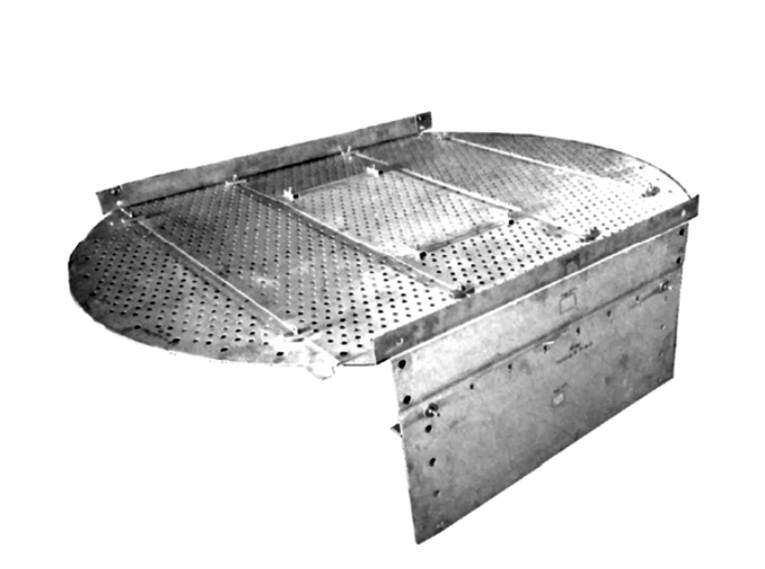
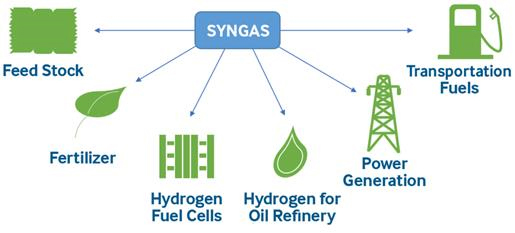