At British Sugar, Cantley, UK, 1,350 tonnes of sugar are produced every day. After the sugar crystals are washed, dried and cooled, they are conveyed to six concrete storage silos, which have a total bulk capacity of 60,000 tonnes. To keep the sugar free flowing, and to avoid clogging during conveying, the climate has to be strictly controlled. The relative humidity in the conveying area needs to be kept below 40% RH, or relative humidity, throughout the year.
Pikatiedot
- Energy consumption reduced by 50%
- Return on investment (ROI) of less than 2 years
- Green Tech energy efficient fan motor
- Flexible fan motor design allows for horizontal or vertical discharge
To control the climate around the conveyor belts and in the silos while securing and maintaining a high product quality, British Sugar is operating seven Munters MX and MXT dehumidifiers. As it’s necessary to give constant attention to measures that can potentially reduce energy consumption and protect the environment, British Sugar has set up a number of ambitious goals on savings. Production processes have already been evaluated and optimised, and the time had come to explore other possible savings. Munters’ UK Service Team was consulted to identify possible energy saving options related to the dehumidification systems. Munters suggested an upgrade of the process air fan, including the 3 Kw AC fan motor. Together with British Sugar, it was decided to do a pilot project, upgrading one dehumidifier to a Munters MXT2800.
Excellent energy savings
Munters’ partner ebm-papst is manufacturing EC (Electronic Commutator) fans. EC is a permanent magnet motor that has an electronically controlled stator field, compared with the voltage induced stator field of an AC induction motor. The EC motor allows proportional control over a 0-100% range with no induction present. This can be via a pressure transducer or manual potentiometer control, either 0-10 vdc or 4-20 mA. Replacing the old and original fan with a 3 Kw motor for an EC fan upgrade, British Sugar is offered the same air volume & static pressure with only 1.6Kw power consumption, which in turn can reduce energy costs by more than 50%. Flexible discharge options The EC fan is very versatile in terms of installation, and it’s designed with removable feet that allow for vertical discharge as well as the standard horizontal discharge. This allows for more possibilities especially in tight installations. A quick return on investment The upgrade process involves the removal of the original square box design fan, ductwork modification, mounting of EC fan assembly, modification of the original process fan switchgear, removal of a process fan contactor and fitting of a potentiometer. Depending on the accessibility of the dehumidifier, the upgrade process amounts to approximately one day of labour. At British Sugar the dehumidifiers are in operation 8,500 hours per year. Based on a price for electricity of 8.5p per kwH, the ROI (return of investment) is less than two years, including all costs for parts and labour. The success of this pilot project will be followed up by upgrading the other six Munters dehumidifiers in operation at British Sugar. Further energy saving options To be able to offer even higher energy efficiency for Munters dehumidifiers, an energy recovery purge on the desiccant rotor (wheel) has been developed. The purge option comes both as a pre-installed feature or as a retrofit to exisiting MX dehumidifiers. Recovering heat from the rotor regeneration process through multiple methods, the energy needed for regeneration is reduced by up to 30%. The principle of the MX Energy Recovery Purge The heart of the Munters dehumidifier is the desiccant rotor which rotates slowly between two primary airstreams - process and reactivation. In the process airstream water vapour is removed as it passes through the desiccant rotor. This dehumidified air is then delivered to the required area of the building. The rotor then rotates into the reactivation sector where a heated airstream is passed through the rotor. The desiccant rotor releases the water vapour to this airstream. This moisture laden airstream is then exhausted outdoors. The majority of the energy required for the desiccant process is used in heating the reactivation airstream. The unique Energy Recovery Purge system acts as an energy recovery system, collecting waste heat off the hottest section of the desiccant rotor and using it to help with the regeneration process. This reduces the energy required for reactivation by up to 30%, while lowering the discharge temperature of the process air, decreasing energy costs for post cooling.
Sovellukset tässä tapauksessa
Pikatiedot
- Energy consumption reduced by 50%
- Return on investment (ROI) of less than 2 years
- Green Tech energy efficient fan motor
- Flexible fan motor design allows for horizontal or vertical discharge
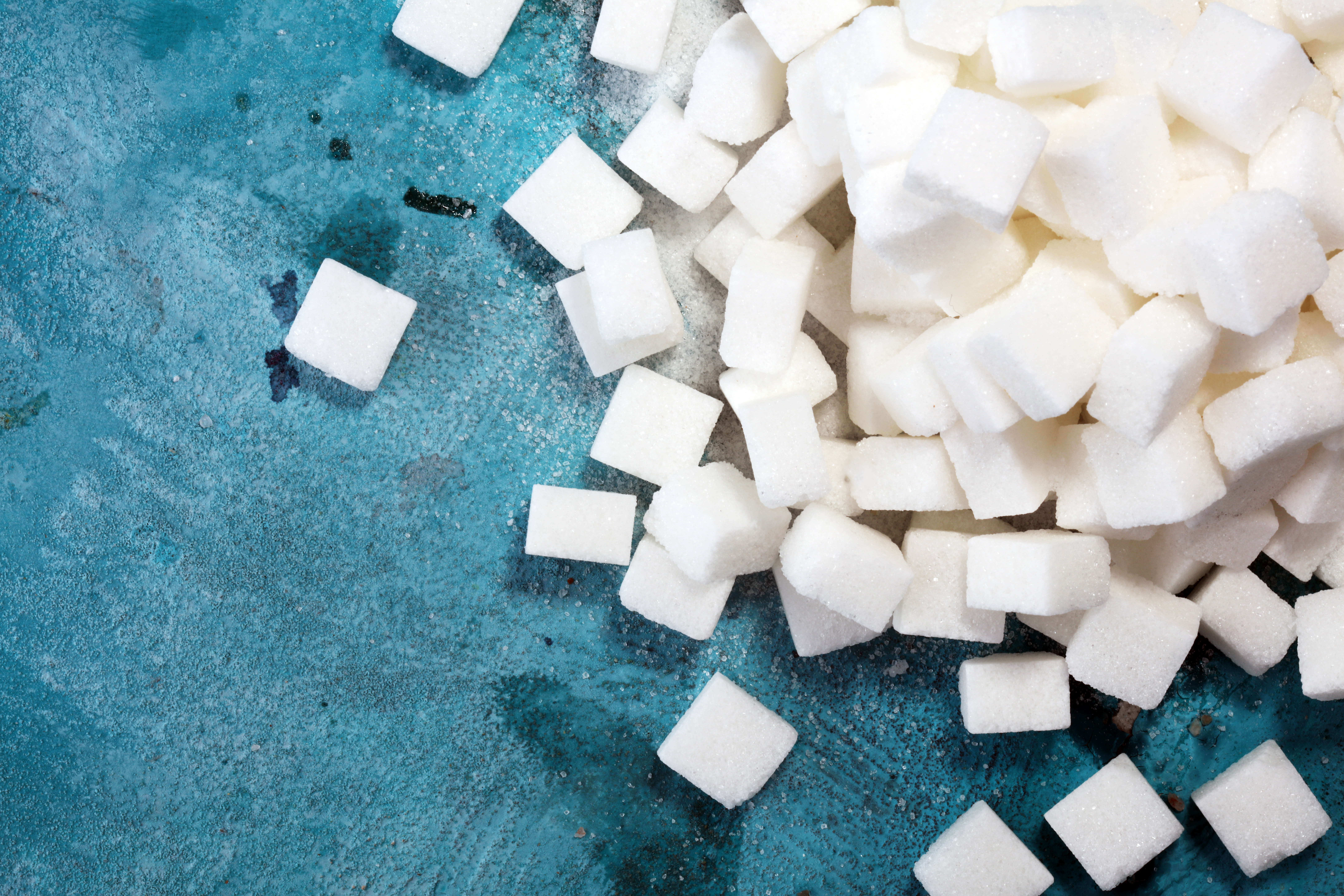
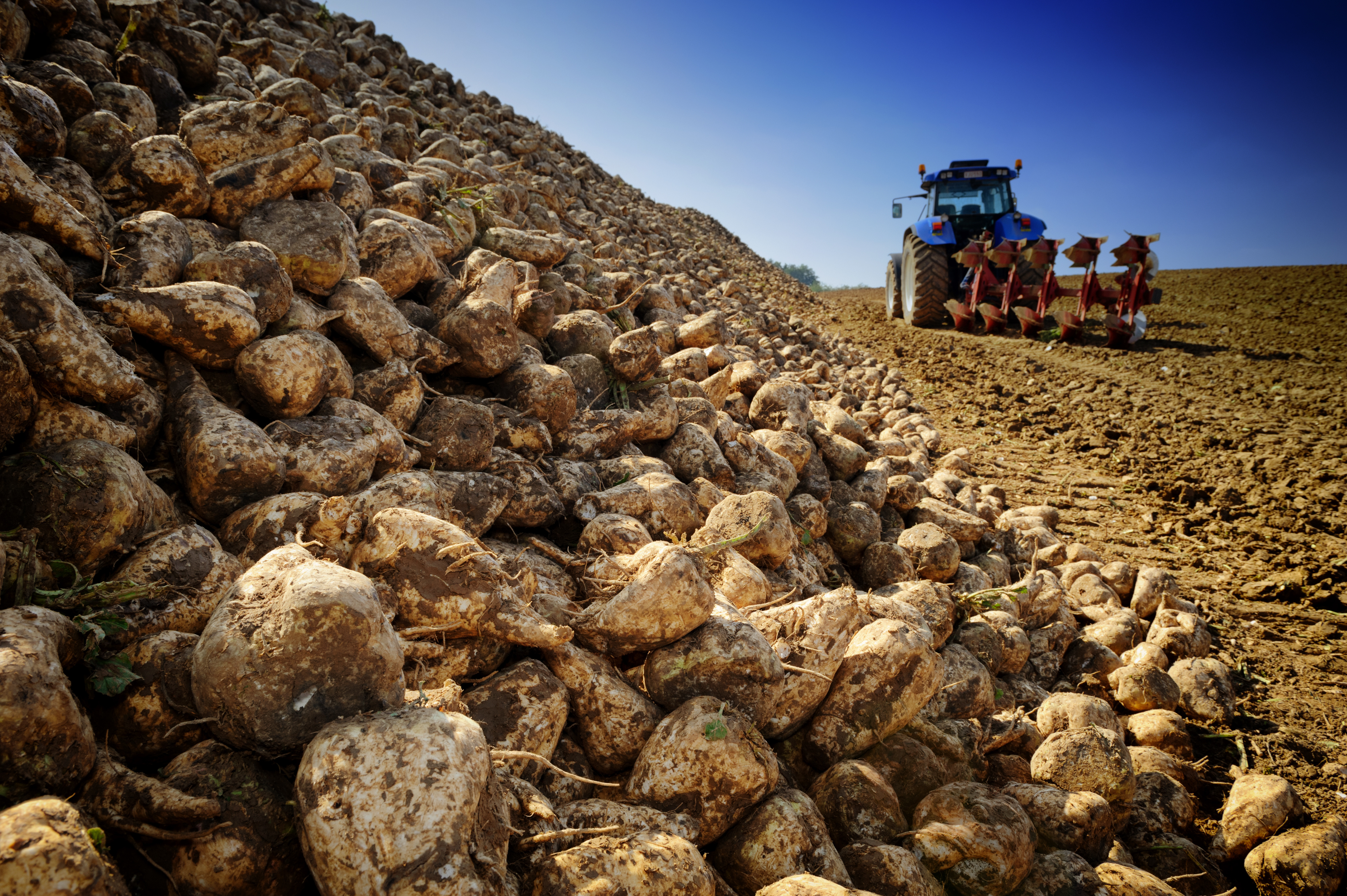
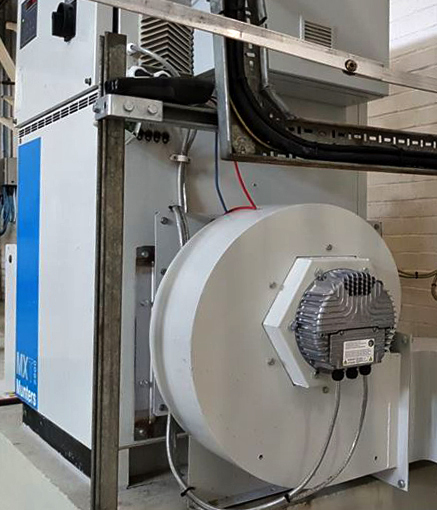
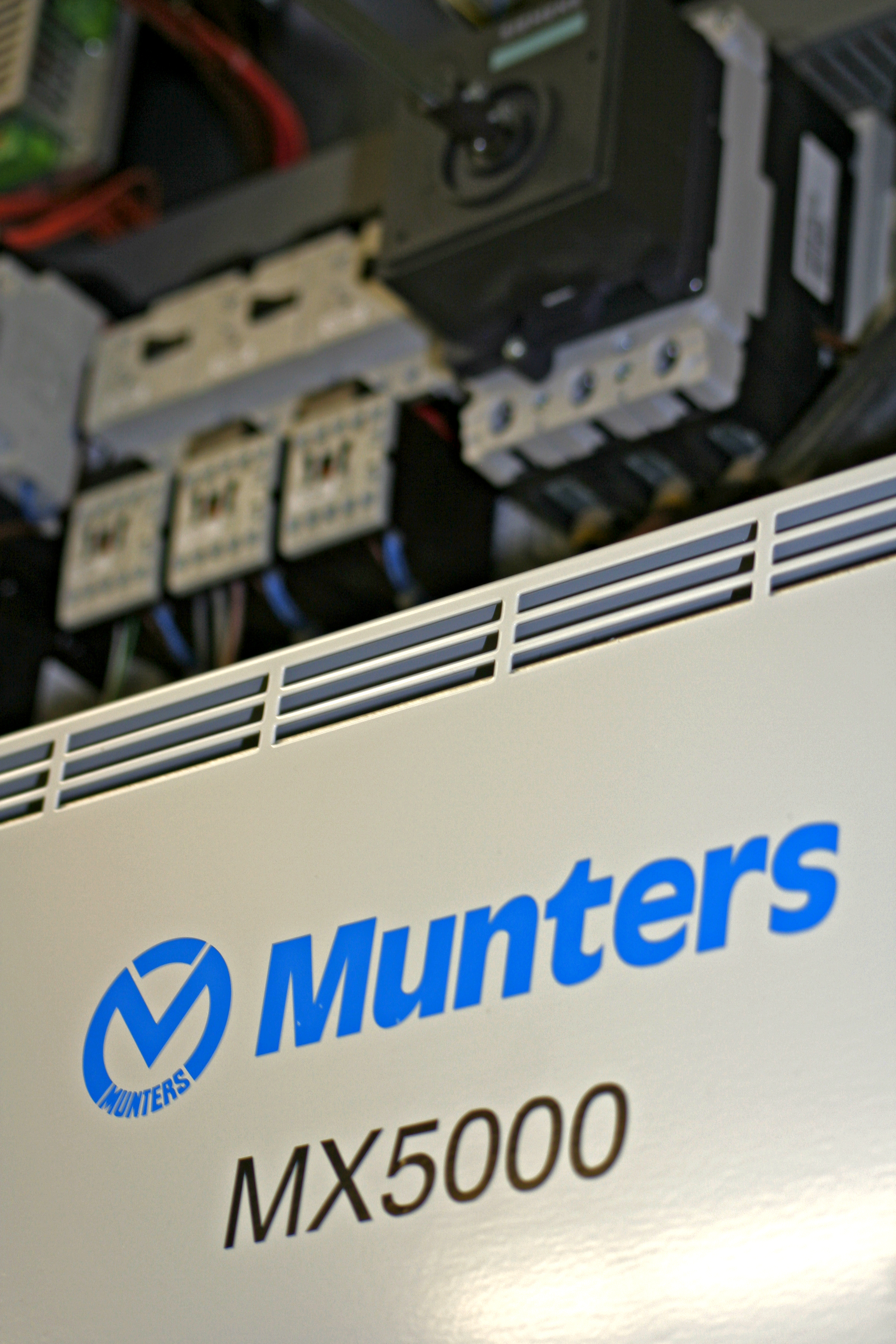
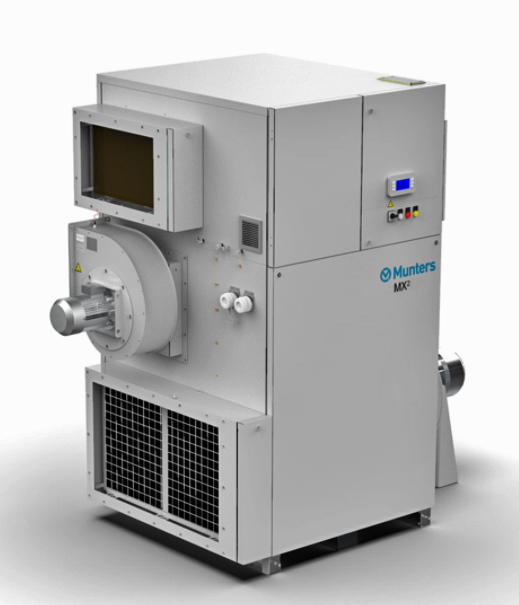
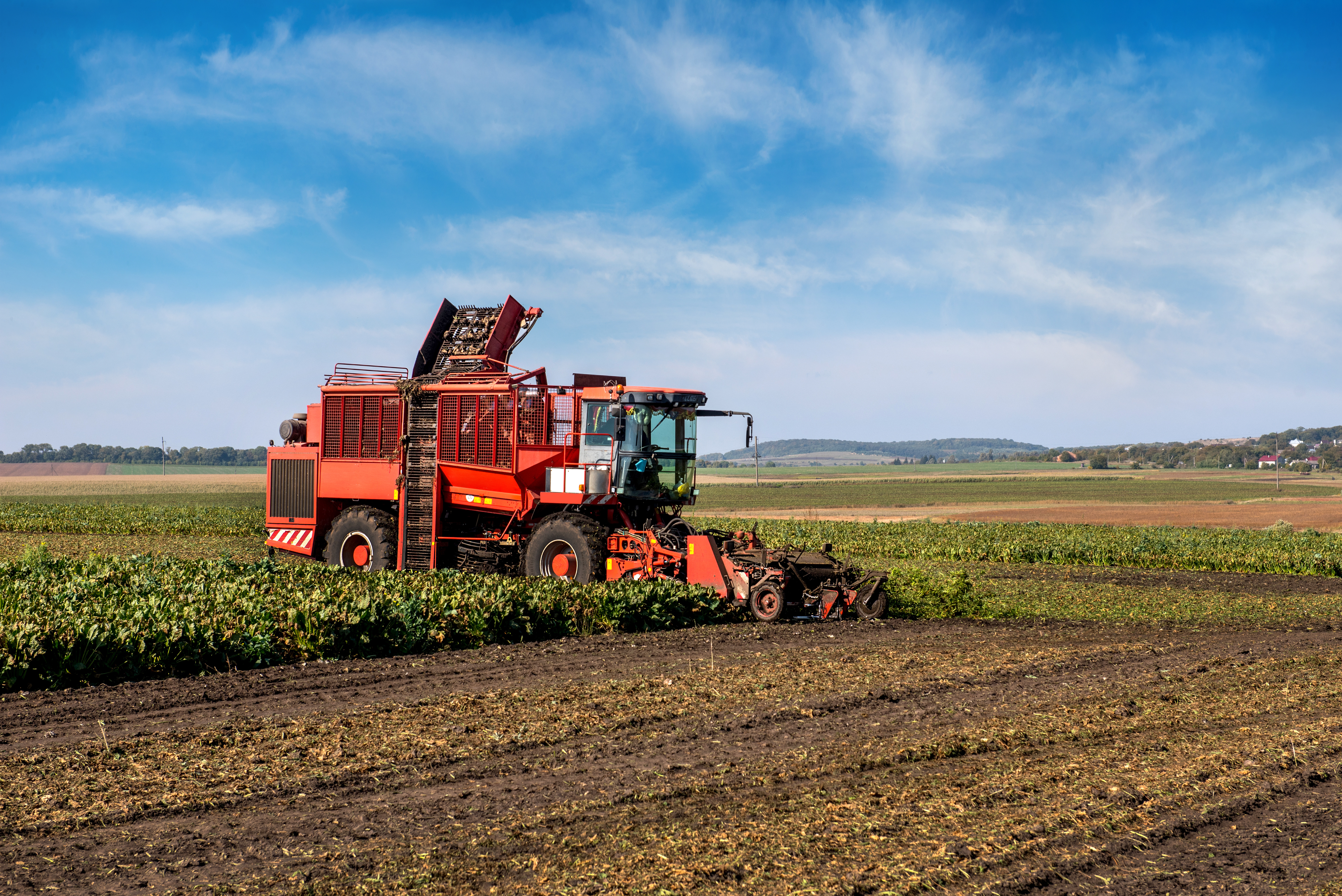
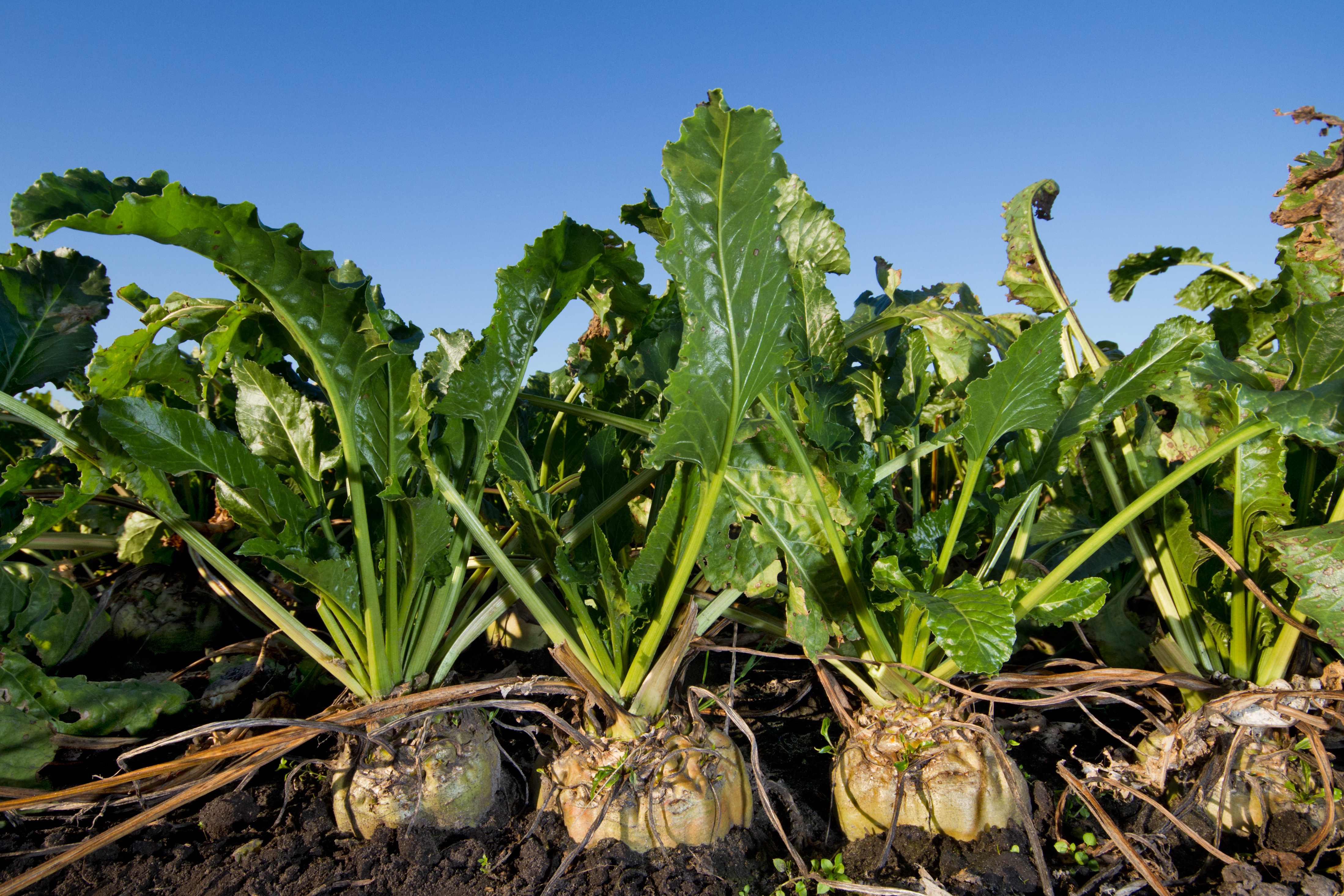