A leading ammonia manufacturer increased their plant capacity by 20% using Munters’ mass transfer equipment.
Quick facts
- Customer: Fertilizer industry
- Location: Western India
- Tower Name: CO2 absorber and regenerator
- Tower Diameter: 4900 mm; 2730-3940 mm
- Mass Transfer Equipment: Tower packing and internals
Background
The customer is a leading manufacturer of ammonia, urea, di-methyl-formamide and ammonium bi-carbonate. Process overview The ammonia and urea production units generate hydrogen (H2), di-nitrogen (N2) and carbon dioxide (CO2) feeds through a common reformer. Outlet gases from the reformer are passed through the absorber, where hydrogen and other light gases are separated, while the carbon dioxide is removed via solution absorption. Hydrogen and other light gases along with slipped carbon dioxide from the top of the absorber are passed to the methanation section. The methanator converts the residual carbon dioxide to methane to increase the catalyst life of the ammonia reactor. The rich solution from the absorber is then stripped in the regenerator, and the carbon dioxide gas is used to produce urea. The lean solution from the regenerator bottom is sent back to the absorber. Customer requirements In existing conditions, carbon dioxide slippage from the absorber was very high (~1200 ppm). This led to an increase in the load on the methanator while increasing the volume of the purge stream from the ammonia loop. The customer wanted to revamp the system to: - Reduce CO slippage - Increase plant capacity without sacrificing absorber efficiency Problem analysis When the existing system was studied, it was noted that the Pall Rings were used as mass transfer media in the packed towers. The Pall Rings have an inherent drawback of higher pressure drop and performance limitations for mass transfer. This resulted in increased compressor load, which led to excess carbon dioxide slippage. Solutions provided Hydraulic rating of existing towers and tower internals was done using Medal-Pak and the following results were noted: - The pressure drop was found to be appreciably lower than that of Pall Rings - The capacity could be increased by 20% - Minor modification of the existing internals to handle higher loads was suggested Based on the process overview it was predicted that carbon dioxide slippage would be in the range of ~ 1200 ppm. Accordingly, Medal-Pak tower packings were manufactured, supplied and installed. The internals were modified on site during the shutdown. Results achieved - CO2 slip decreased to 500 ppm at higher capacity of 105% - Steam consumption in re-generator decreased to 10%
Quick facts
- Customer: Fertilizer industry
- Location: Western India
- Tower Name: CO2 absorber and regenerator
- Tower Diameter: 4900 mm; 2730-3940 mm
- Mass Transfer Equipment: Tower packing and internals
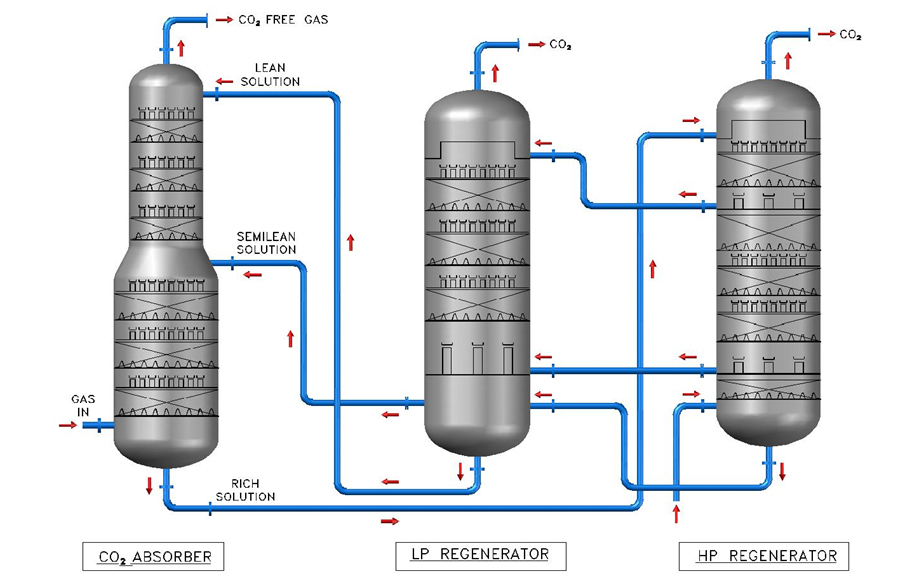
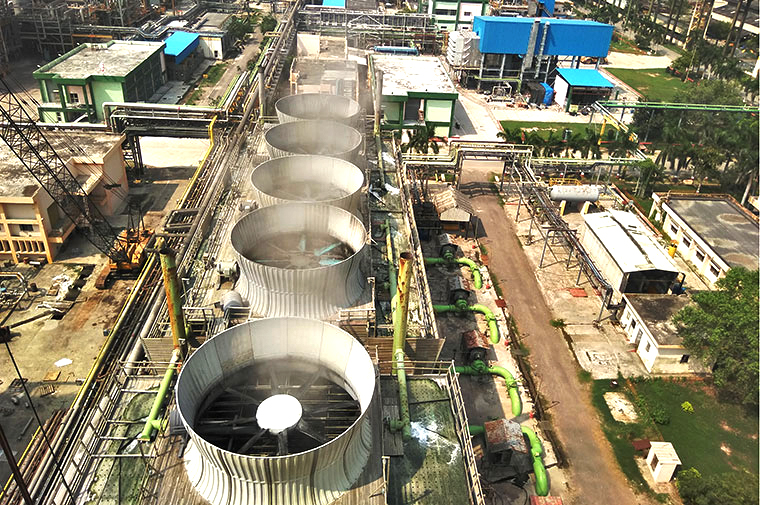