The Belgian company Niko NV delivers more than 5000 products and solutions for switching materials, door communication systems, lighting control and home automation systems. It has branch offices in Europe and a wide network of agent and distributors. At Niko’s Belgium manufacturing plant attention is paid to control and minimize environmental impact and reduce energy consumption. Munters MDS1500 desiccant dehumidifier was installed in the 90’s to provide dry air to a galvanized plate drying process after they are treated in a zinc bath. The MDS unit has an airflow of 15,000m³ and is running 12 hours a day, 5 days a week.
Quick facts
- ROI in only 20 months
- Shorter drying times, increasing production capacity
- Utilizing warm wastewater to reduce rotor regeneration costs
- Internal Rotor Energy Purge for further heating cost savings red
- Control system update enables communication with BMS system
Refurbishment paying off
A recent performance check-up of the MDS unit determined that a refurbishment of the unit would lead to improved dehumidification capacity and significant energy savings. Munters Belgium presented a plan to refurbish the MDS unit, which has been implemented. As the capacity of the rotor (desiccant drying wheel) had dropped significantly over the years of daily use, galvanized plate drying time was no longer optimal. By replacing the rotor, plate drying time has been significantly shortened. Restoring the original unit performance grants annual savings of € 25,000/year.
Range of energy saving measures implemented
Niko NV has access to 50°C warm water from cooling compressors, water that had been treated as waste water. The MDS dehumidifier is now equipped with a coil for air stream pre-heating, which is used for regeneration of the desiccant rotor. Utilizing the warm wastewater for the heating coil will ensure a reduction in cost of approximately € 10,400/yr. An internal heat recovery purge sector (Energy Recovery Purge) has been added and works by recirculating the air into the regeneration cycle after the heater. This energy saving feature will save an additional € 2,200/year. Stable future operations secured The refurbishment also includes a complete update of vital components, such as fan bearings, drive motor, belts and sealings, ensuring that the operation will remain reliable and trouble-free for years to come. Continuously working on optimizing both dehumidification capacity and energy efficiency, Munters is also very much focused on using the best possible control systems to easily control and monitor the dehumidifiers and other air treatment solutions. The MDS at Niko’s manufacturing facility has now been updated to a new Climatix control that´s integrated with the BMS (Building Management System). The upgrade offers control system performance improvements, which make it possible to handle additional energy saving components like the purge and the pre heater. Furthermore, the electrical cabinet was updated to include modern components for optimal control of the airflow and BMS communication. ROI in only 20 months The improved energy efficiency and higher rotor capacity will ensure annual savings that gives Niko a ROI (Return of Investment) in only 20 months. Besides the quick ROI, Niko also benefits from the significantly higher production capacity - an amount NOT included in the ROI calculation. Following the refurbishment, the MDS unit’s vital parts are all new and the unit is expected to deliver the required climate conditions in the production area for many years to come. Munters Belgium is a trusted service partner with Niko. During annual service visits the performance and operation of the MDS unit will be closely monitored. Regular replacement of consumable parts, such as filters, will be taken care of by Munters’ service engineers, which will perform the scheduled maintenance on site.
Quick facts
- ROI in only 20 months
- Shorter drying times, increasing production capacity
- Utilizing warm wastewater to reduce rotor regeneration costs
- Internal Rotor Energy Purge for further heating cost savings red
- Control system update enables communication with BMS system
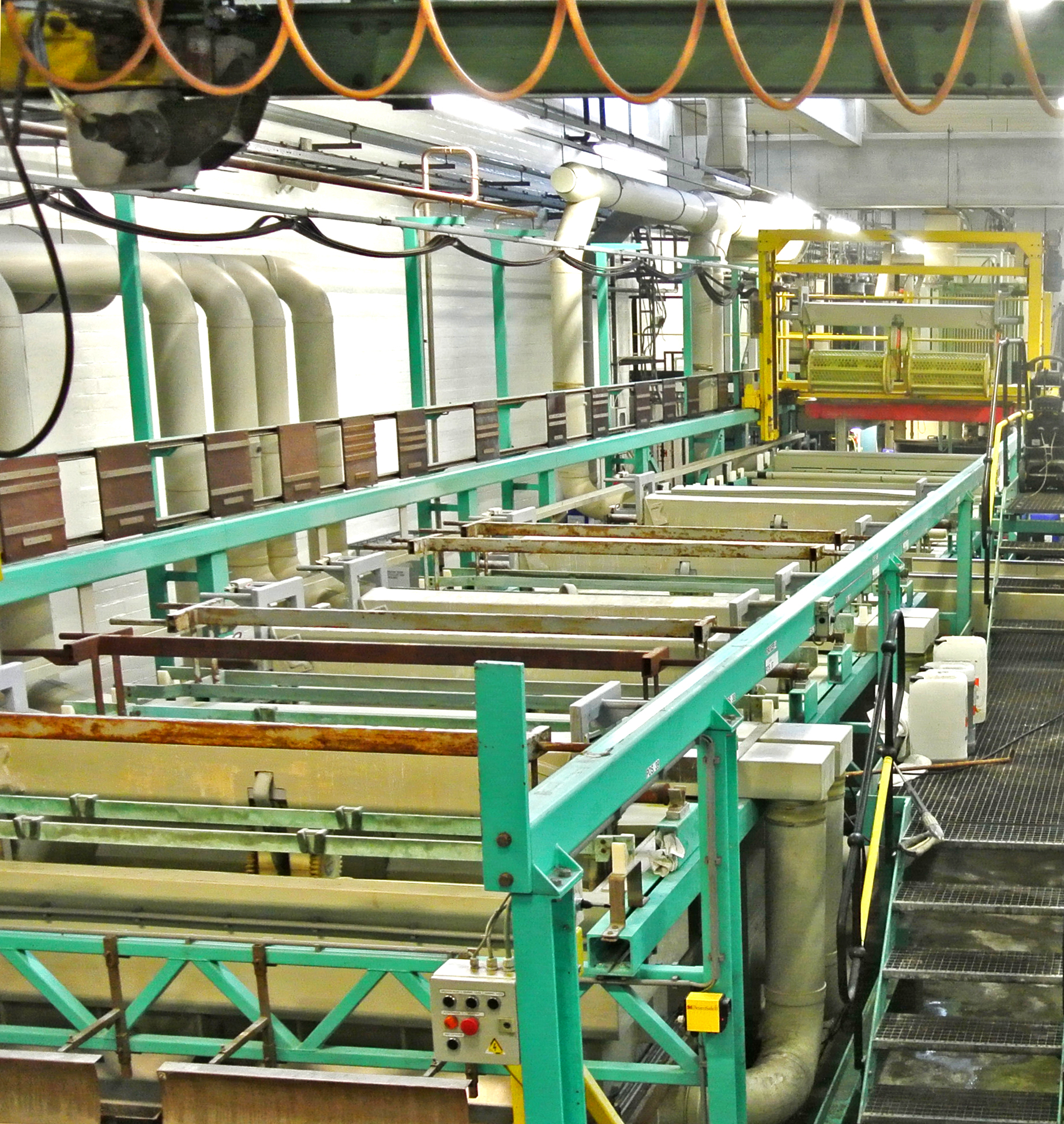
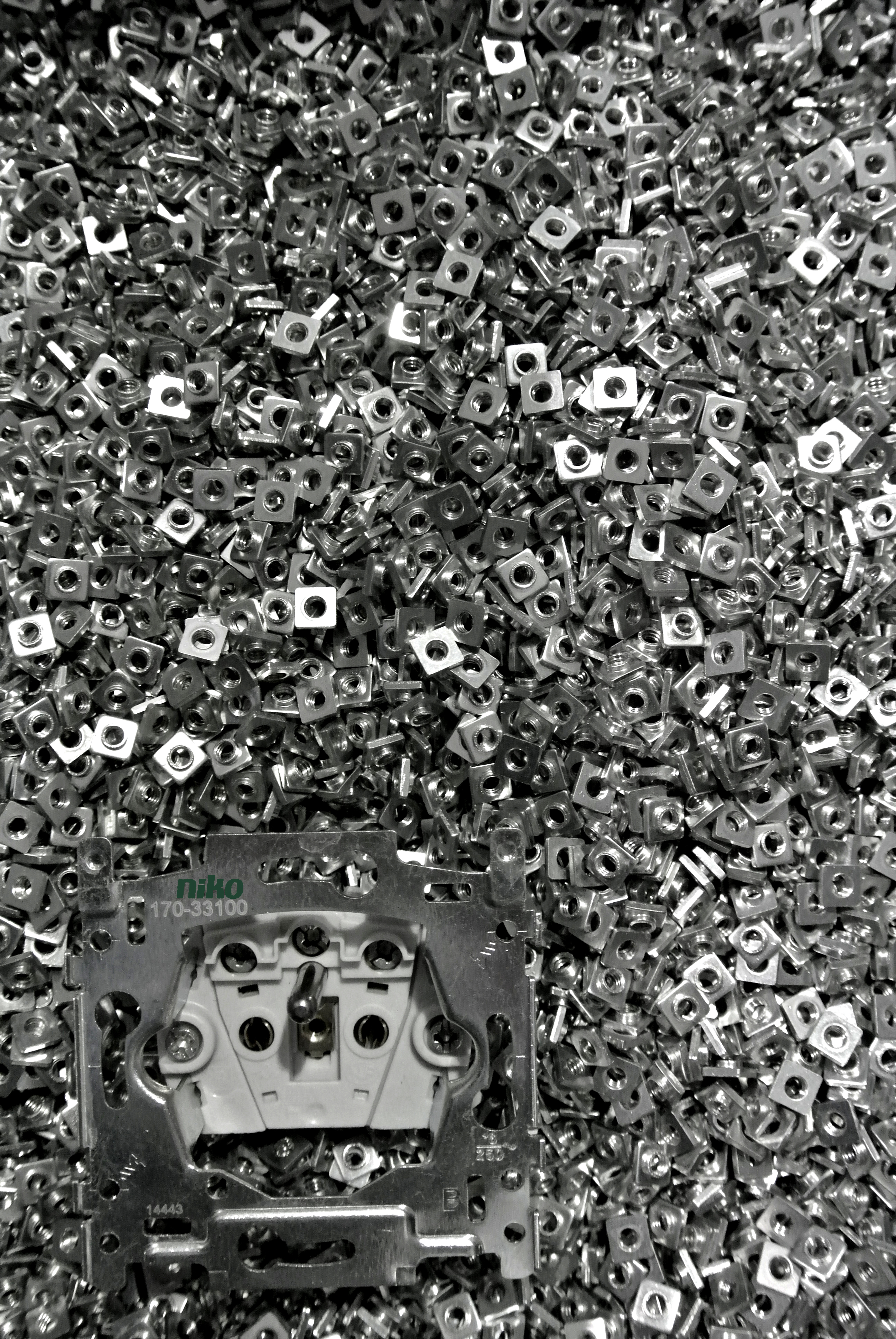
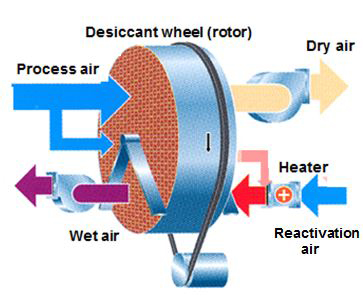