The right climate for pharmaceutical production
The production of critical formulations in pharmaceutical and nutraceutical manufacturing requires precise humidity control and a perfect climate. For quality, energy efficiency, and stable, long-lasting performance, secure your process and production targets with a Munters humidity control system.
Applications for pharmaceutical and nutraceutical industry
Processing
One of the most effective ways to protect raw materials and products during manufacturing, storage, and transport is to control the surrounding environment. The key is to regulate, monitor, and maintain optimal humidity levels continuously, throughout all production processes, from raw material to end-product.
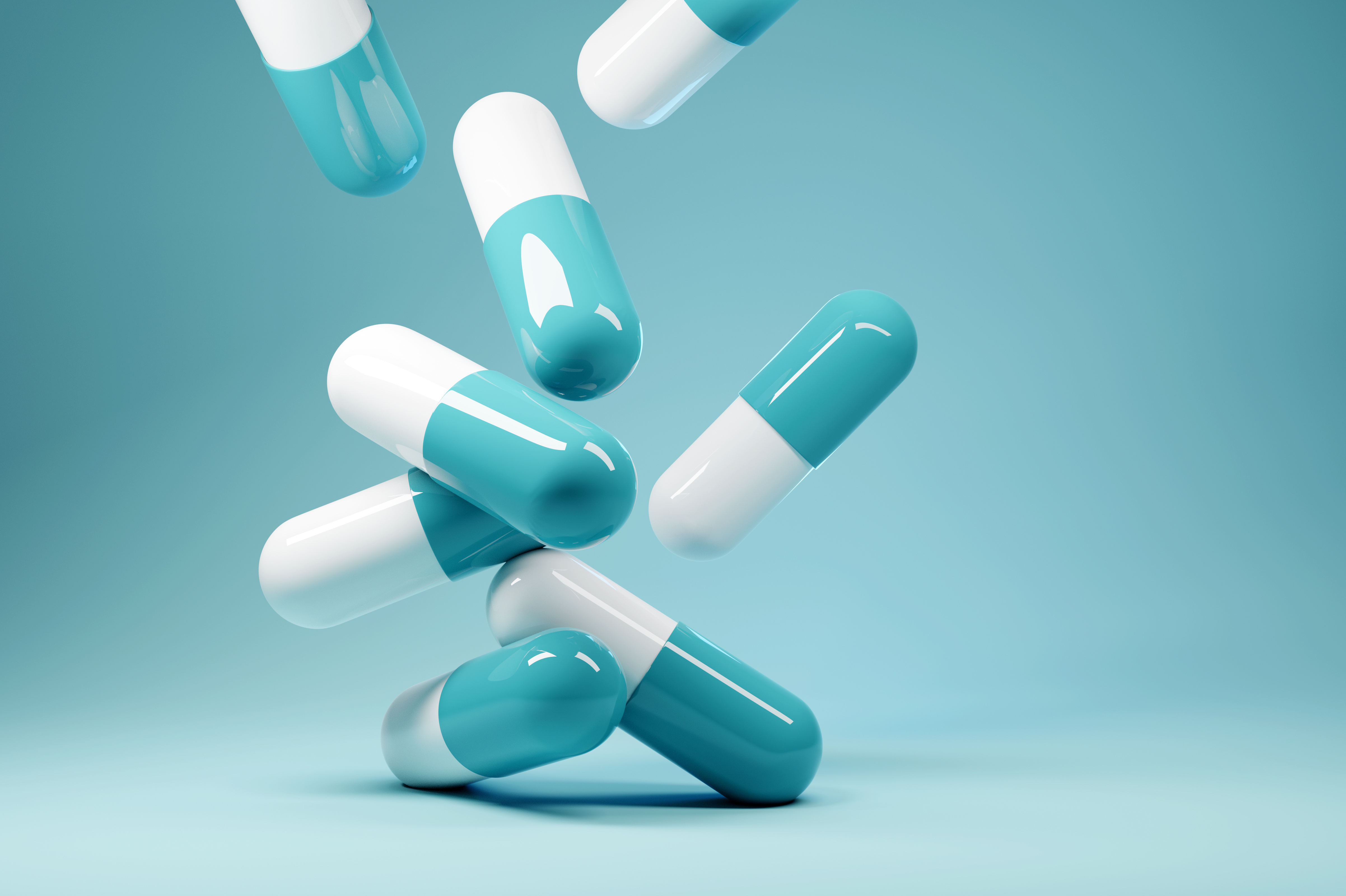
Storage of ingredients
Stable humidity control in dry storage areas helps prevent condensation, improves powder flow, and reduces the need for frequent cleaning.
Storage of products
Every effort must be made to maintain quality and efficacy until the product leaves the plant. Providing low-humidity air to cold storage areas prevents ice, frost, and fog, and improves worker safety. After production, dried capsule shells are vulnerable to the effects of fluctuating humidity, which can compromise their mechanical strength and appearance. A stable climate during packaging and storage minimizes these risks.
Humidity control systems help ensure the proper conditions for softgel and hard-capsule drying. Ideal air quality helps ensure that softgels dry quickly and meet quality standards. Munters can provide precise drying conditions for pharmaceutical products, whether gelatin, hydroxypropyl methylcellulose (HPMC) or other formulations. Proper humidity control can protect the moisture content of both filled and empty capsules.
Optimal environmental conditions ensure that excipients and APIs can be continuously and reliably blended, while preventing excess moisture from affecting the mechanical and chemical properties. The right balance of moisture keeps granulating mixture in equilibrium with the air around it, maintaining the moisture content required for granules to form.
Maintaining the specified humidity set point results in higher throughput, prevents product sticking, and reduces stoppage and waste. It also cuts energy consumption and improves dosing accuracy.
Smooth coatings with a consistent thickness offer proper dispersion characteristics and maximum visual appeal. Prevent coating problems, such as roughness or ‘orange peel’ defects, blistering, hazing, sticking, picking, and erosion, by selecting and providing the right drying conditions.
Along with tablets and capsules, surrounding air also gets sealed into blister packaging. With the right humidity level, packaged products will be more durable and longer-lasting. During the blow-fill-seal packaging process, condensation on cold surfaces can cause imperfections that affect appearance and structural integrity. Controlling the dew point of the air that surrounds the packaging during the blow-forming process can prevent condensation.
Biologics, vaccines and parenteral products
Product quality depends on manufacturing in a clean, controlled area. Relative humidity (RH) exceeding 70% increases the potential for microbial growth. Proper humidity control reduces drying time following cleaning operations and the vials’ final was.
Clean room and R&D labs
Everything in a clean room and research and development laboratory must be accounted for and within specification, including the purity of the air. Without proper humidity control, the exterior climate can affect room conditions. Maintaining the right humidity levels helps optimize cleaning and sterilization of cleanrooms and equipment.
Removing moisture from the air before hydrogen peroxide vaporization increases saturation levels, providing the highest efficacy. After cleaning, introducing dry air accelerates the drying process, making it possible to return the cleanroom to operation more quickly.
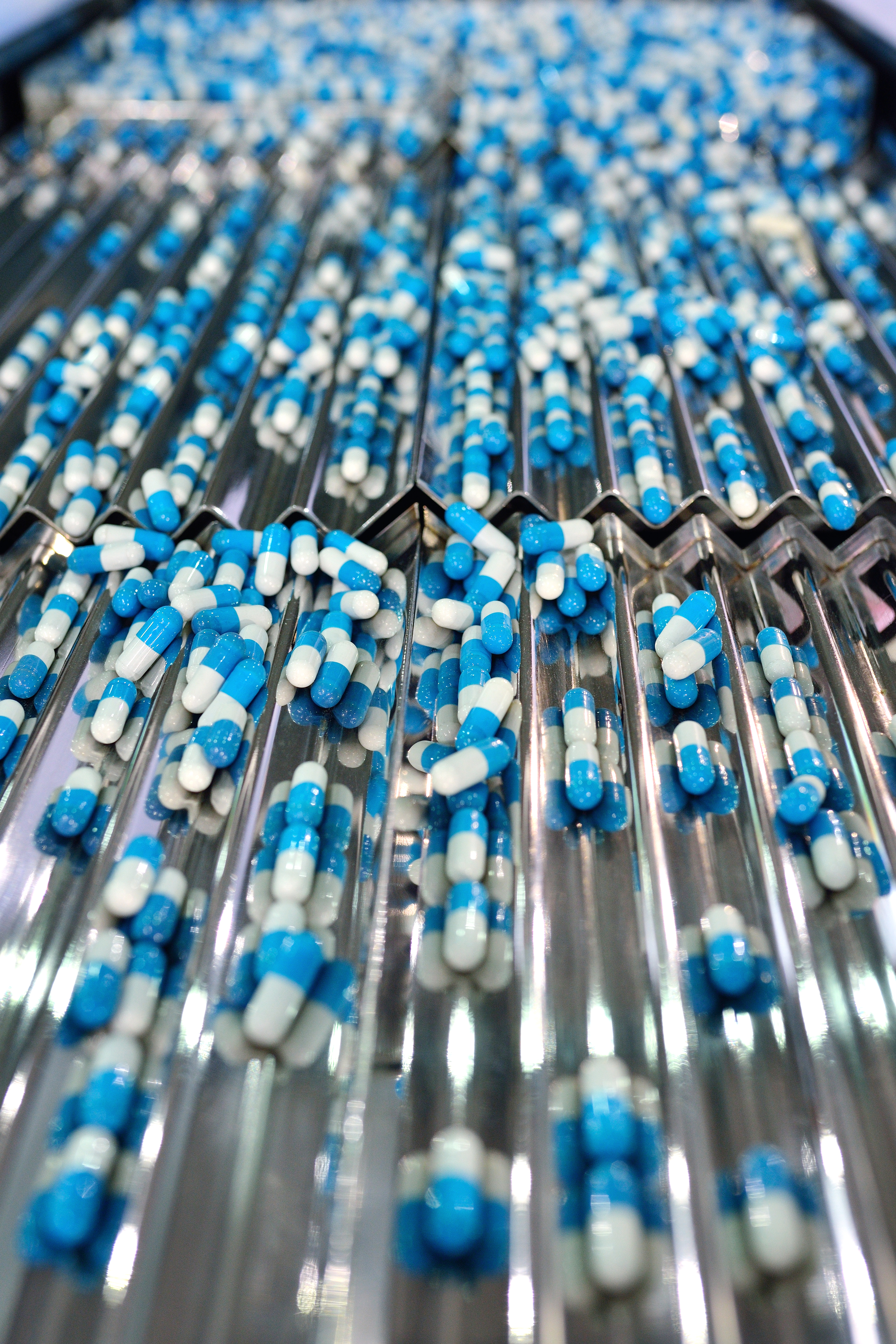
Precise and consistent humidity control
Munters provides a range of humidity control solutions for the pharmaceutical industry, for use throughout the development and production of active pharmaceutical ingredients (APIs). These humidity control solutions provide stable environmental conditions, regardless of the weather or season, and ensure compliance with your air-quality requirements for fixed airflows and HEPA filtration.
Dehumidifiers can control the relative humidity levels of isolators and glove boxes, and can help fine tune humidity, contributing to the production of stable pharmaceutical and nutraceutical formulations.
Munters can provide custom-designed humidity control solutions for every single area of pharmaceutical and nutraceutical production, from small R&D labs to commercial processing lines at large manufacturing facilities. Whether in silos, production facilities, warehouses or transport, humidity is consistently and precisely controlled.
Our humidity control solutions incorporate environmentally friendly technology, providing considerable energy and cost savings. Our market-leading service offering ensures that Munters equipment always delivers the right conditions over its entire life cycle. Continuously maintaining humidity control and GMP-specified climate levels significantly improves production capacity and hygienic processing and packaging conditions.
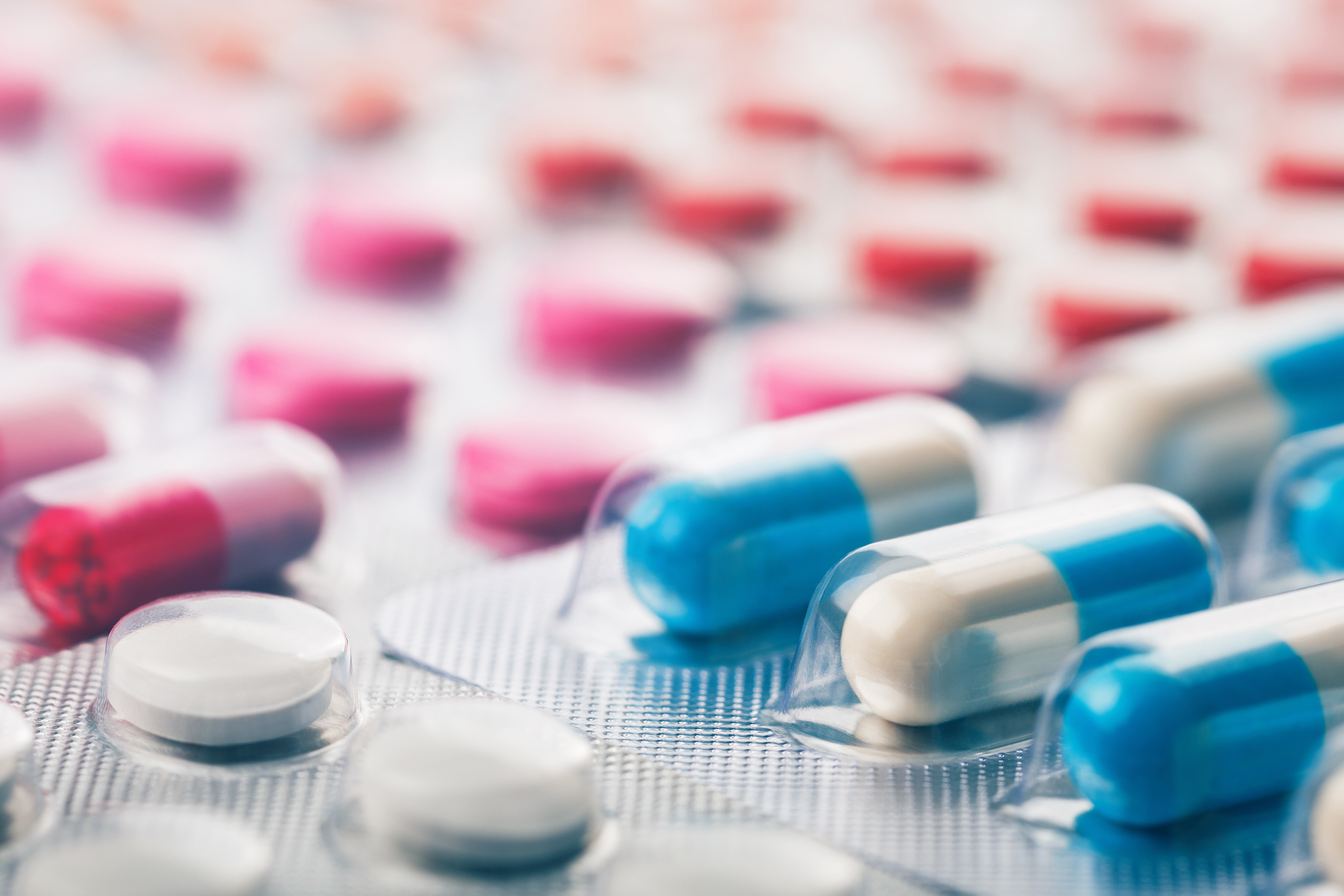
Tableting and Compressing
In the world of sensitive products, powders, and tablets, maintaining their quality and shelf life is crucial. Unfortunately, exposure to high humidity can lead to a range of issues, from clumping and mold formation to breakage, causing interruptions in production and clogging machinery.