Increase manufacturing quality with humidity and emissions control
Semiconductor manufacturing requires closely controlled, dry conditions. Munters desiccant dehumidifiers provide precise humidity control, creating ideal manufacturing conditions for manufacturing and assembly.
Excessive moisture in the air causes corrosion of circuit points, condensation on microchip circuit surfaces and improper adhesion of photoresists, causing operational failure of the semiconductor assembly process.
Munters world-leading desiccant rotor dehumidification systems effectively remove moisture from the air, enabling precise and consistent humidity control in your dry rooms and clean rooms.
Moreover, Munters energy-efficient zeolite adsorption technology captures and treats volatile organic compound (VOC) emissions from semiconductor production processes. Preventing the release of these emissions into the atmosphere helps protect human health and the environment.
Applications in semiconductor manufacturing
Assembly area
Excessive moisture can adversely affect the bonding process during semiconductor and integrated circuit production and increase defects.
Masking circuit lines for the etching process with photosensitive polymer compounds called photoresists helps ensure effective bonding.
Due to its hygroscopic nature, this material absorbs moisture resulting in cutting or bridging the microscopic circuits, which can cause component failure.
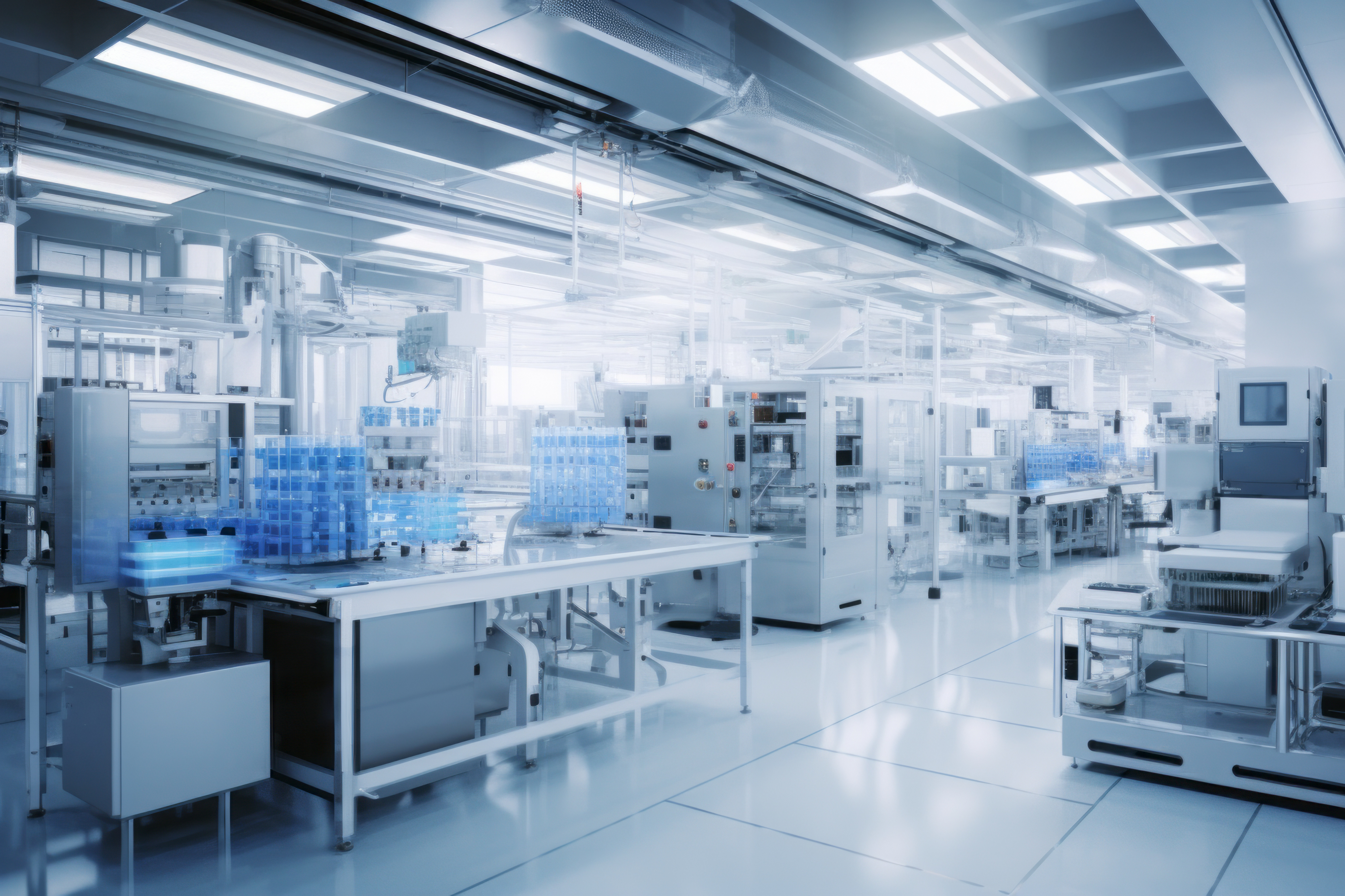
VOC abatement for semiconductor manufacturing
Besides creating optimal air conditions, Munters offers a range of VOC abatement products to clean exhaust air laden with volatile organic compounds (VOCs).
The semiconductor manufacturing process produces VOC-rich exhaust air. These compounds harm human health and the environment and must be reduced before releasing exhaust air into the atmosphere. A VOC rotor concentrator helps reduce emission reduction costs by effectively concentrating the VOCs before abatement.
Advantages:
- High destruction efficiency
- Protects the environment
- Helps meet legislative requirements
- Healthier work environment
- Significantly lower fuel and electricity costs
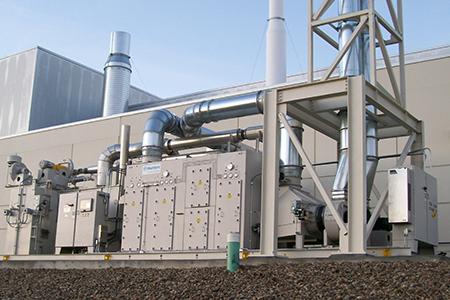
Epitaxial equipment protection
Water vapor or moisture condenses on chilled surfaces of epitaxial equipment, causing components to corrode, resulting in slower processing and operational failure.
Advantages:
- Precisely controlled conditions
- Higher quality
- Improved consistency
- Faster production
- Lower operating costs
Wafer fabrication area
Spinners spray developer on the wafer surface during manufacturing, causing the solvent to evaporate quickly, cooling the surface.
As a result, water vapor in the air condenses on the wafer surface. As condensation forms on the wafer, the characteristics of the developer begin to change. Moisture absorption also causes the polymer to swell.
Controlling relative humidity reduces the dew point of the ambient air, eliminating condensation on the wafer’s surface and preventing failure and spoilage.
Faster vacuum pump-down
Excessive humidity levels cause vacuum equipment, like cryopumps, to slow operation due to the large water vapor load.
Reducing the relative humidity levels increases batch processing speeds, improving productivity.
Photolithography room
Excessive humidity in a photolithography room causes the silica to absorb moisture, resulting in improper adhesion of photoresistors, which causes stress fractures and surface defects.