A major OEM oxidizer based out of Ft. Lauderdale, Florida required a heat exchanger for a catalytic oxidizer system to be sold to Andrx Pharmaceuticals, which had hazardous airborne contaminants that needed to be exhausted out of the production area. The process airstream went through an oxidizer system to remove 99% of airborne contaminants before the airstream was vented into the atmosphere. The heat exchanger needed to use exhaust air heat to maximize oxidizer energy efficiency. A Munters’ Thermo-Z heat exchanger was chosen as a pre-heater in the system to provide energy savings by taking the 1200ºF exhaust air temperature and using it to preheat the 100ºF inlet air temperature to approximately 650ºF.
Quick facts
- Custom small footprint design
- Multiple stacked heat exchangers within a single outside casing
- Welded design with almost zero leakage enables oxidizer to reach high destruction efficiencies
Finding the perfect fit
The application needed 60,000 cfm airflow, which normally entails large multiple counterflow units. However, space was limited so the size of the footprint was a significant concern. The challenge was to find a counterflow unit that would fit within the OEM’s footprint limitations while still meeting their performance requirements. A Munters’ double-stacked design was the answer. Two identical counterflow units were stacked so the system footprint was the size of a single unit, roughly half the typical footprint. The design required a great deal of internal and external structural support and specially designed plenums to direct the air to the inlets and outlets.
A successful relationship
The net result was a cost-competitive, well-designed industrial heat exchanger that provided the smallest available footprint in the industry with similar unit performance. Munters met and conquered the challenge presented by the OEM. This is one of four Thermo-Z heat exchangers being used together with oxidizers at Andrx Pharmaceuticals. Due to the success of these projects, a fifth Thermo-Z installation is underway at this location and three to four more units are to be installed at a North Carolina site. Munters innovation helped to secure a long-term future with this OEM and develop a unique design in the high-temperature energy-recovery industry.
Quick facts
- Custom small footprint design
- Multiple stacked heat exchangers within a single outside casing
- Welded design with almost zero leakage enables oxidizer to reach high destruction efficiencies
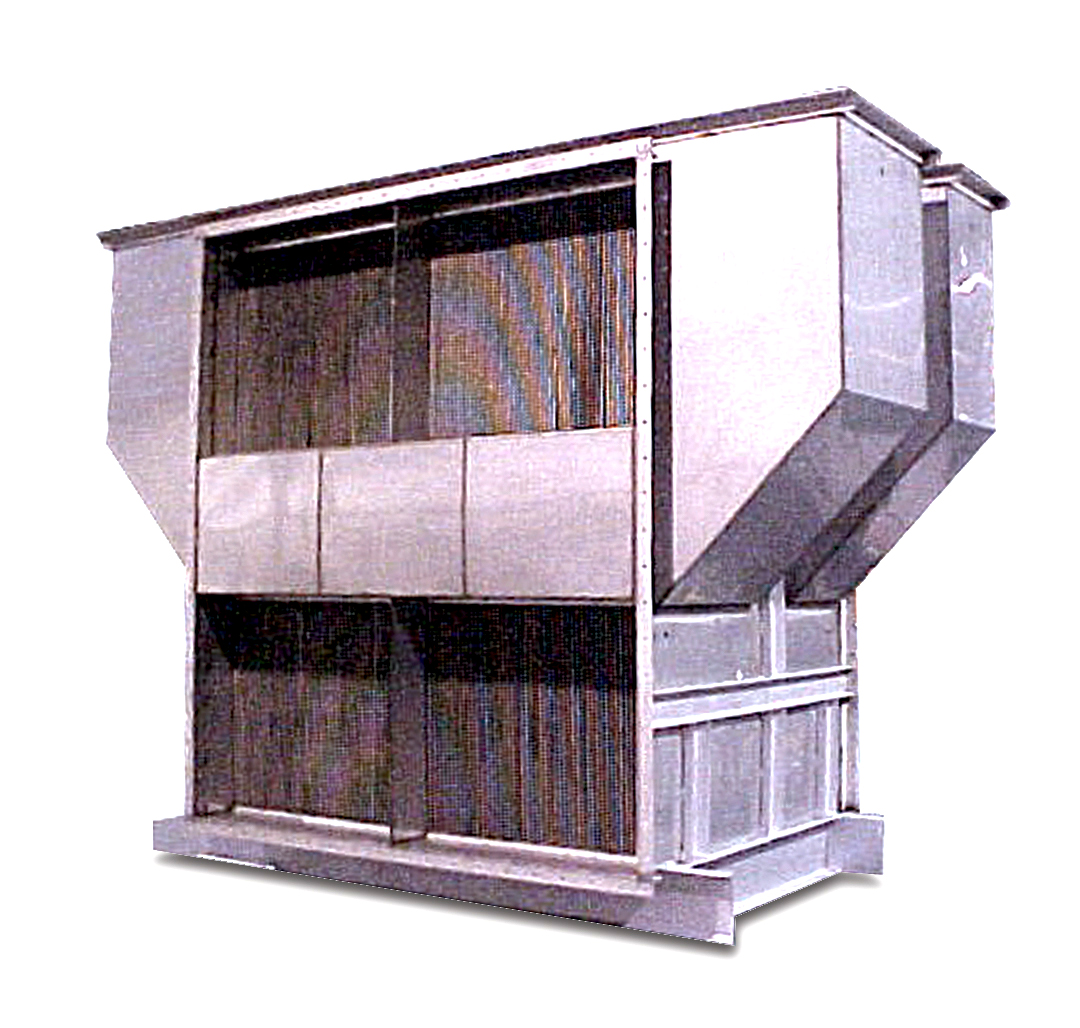
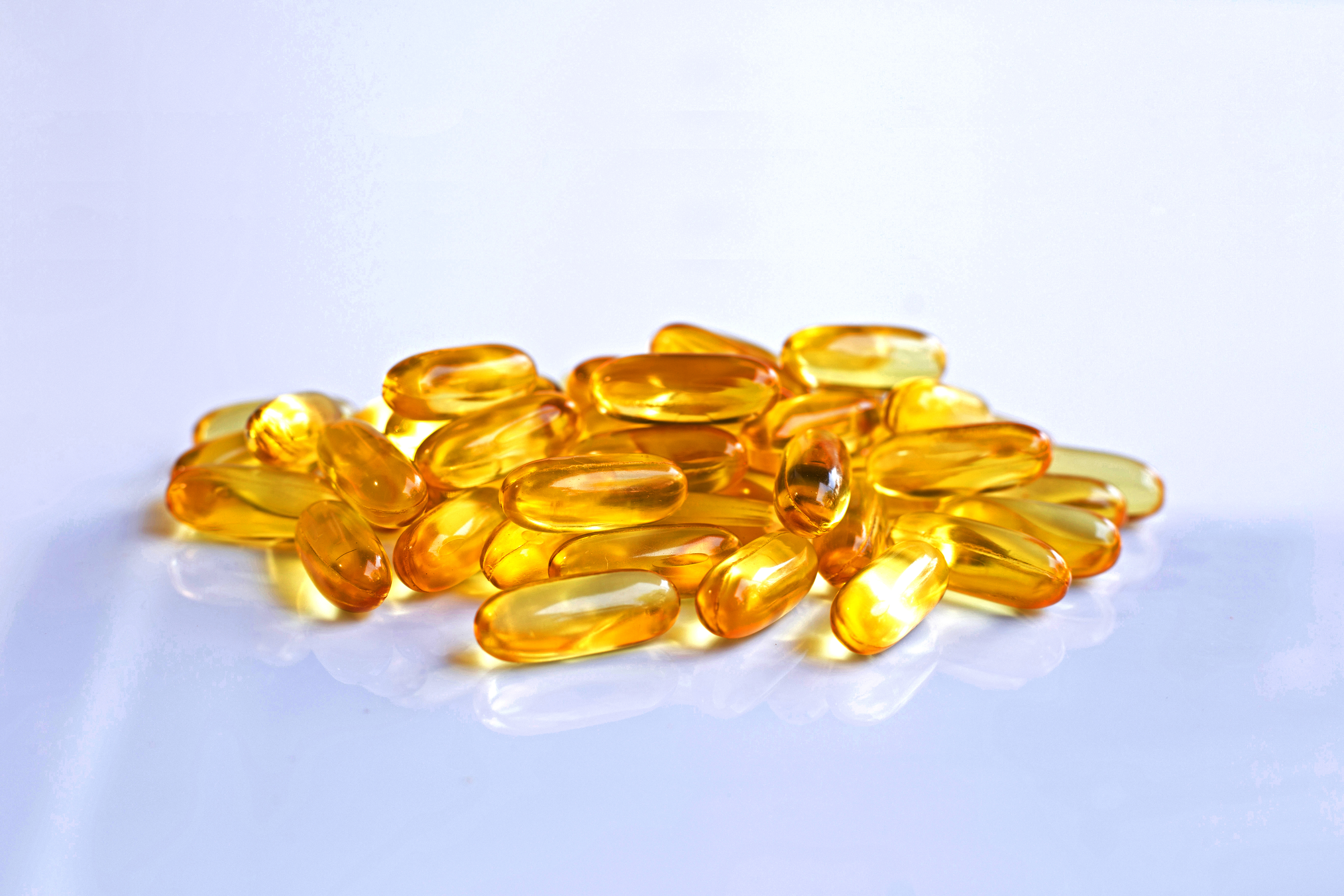