Based in Orlando, Florida, Crawford Equipment & Engineering offers a complete line of services related to industrial process heating equipment, including design, fabrication, and sales. Their diverse offering is often supported by Munters air-to-air heat exchangers. The company installed a unique, two-stage energy recovery system for a well-known automotive parts manufacturer that fabricates headlight lenses.
Quick facts
- Eliminate boiler capital costs
- Provide a smaller carbon footprint
- Lower plant operating costs
Plant process supported by Munters
One of the plant processes involves applying a chrome coating to the lenses. A thermal oxidizer incinerates isopropyl alcohol, and the butyl acetate fumes the output. A Munters Thermo-Z heat exchanger recovers heat from the incinerator’s exhaust at 1400°F, which preheats inlet effluent air from 123°F to 1180°F. During this process the heat exchanger operates at 83% efficiency, which is extraordinary.
Big savings thanks to Munters
During the second stage, also supplied by Munters, a water coil in the exhaust stream uses 366°F air coming out of the first stage heat exchanger to heat a water-glycol mix from 160°F to 190°F. The water then flows to a cleanroom in the plant, where a forced air fan blows ambient air across a second coil, heating the air from 70°F to 180°F. This hot air flows to a flash-off zone, where it cures a sprayed-on clear coat and solvent applied to the lenses. Using waste heat from the thermal oxidizer to heat water in this fashion eliminates the need for a boiler, providing the customer with significant savings.
Quick facts
- Eliminate boiler capital costs
- Provide a smaller carbon footprint
- Lower plant operating costs
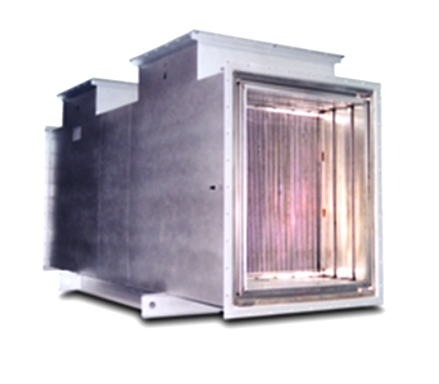
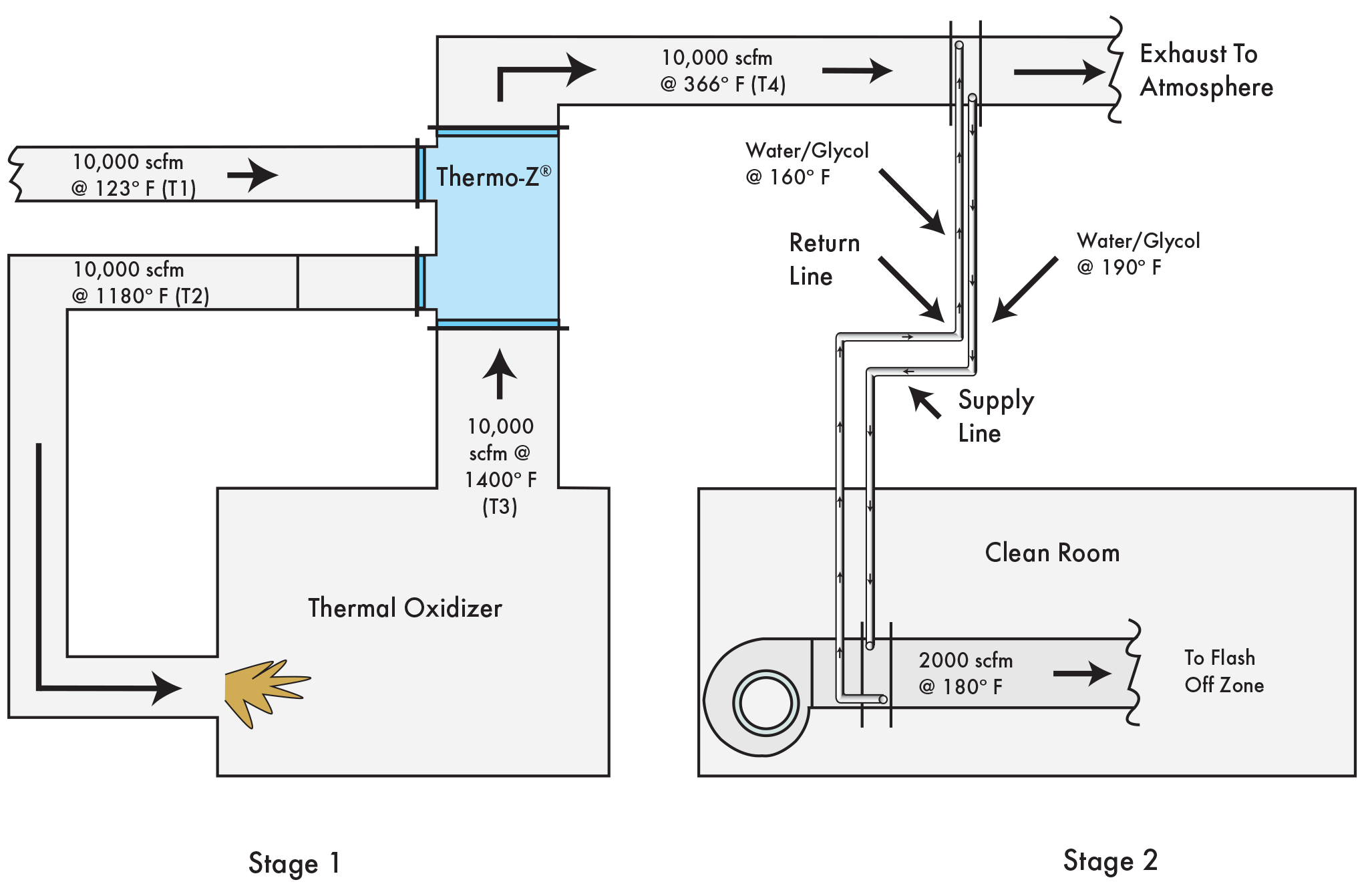