A leading manufacturer of petrochemicals in India reduced their LAB slippage to less than 5% and improved its Acid Color Index, which measures the quality of the LAB, to desired levels using Munters’ mass transfer equipment and service.
Quick facts
- Customer: Petrochemical industry
- Location: Western India
- Tower Name: Paraffin recovery unit
- Tower Diameter: 1200 mm to 4500 mm
- Mass Transfer Equipment: Random packing (Medal-Pak) and tower internals
Process overview
LAB (Linear Alkyl Benzene) is the reaction product of n-paraffin and benzene. The LAB plant consists of a PACOL unit (reactor) and recovery unit (paraffin column, re-run column and recovery column). The output from the reactor consists of un-reacted paraffin, LAB and HAB (Heavy Alkyl Benzene), which forms the feed to the paraffin column. The paraffin column separates the un-reacted paraffin from the product and by-product: LAB and HAB. The re-run column in the loop then separates LAB and HAB. Further in the recovery column LAB, which has slipped along with bottoms of re-run column, is separated out. The LAB extracted from the re-run and recovery column need to be of high purity and have the desired Acid Color Index (ACI). Customer requirements - Maximize recovery of LAB thereby limiting the slippage to < 5% - Improve Acid Color Index to a range of 20-25 Acid Color Index is the measurement of LAB purity. LAB is mixed with 98% sulphuric acid (H2SO4) and the color index of the LAB sulfonate is measured. Good quality sulfonate (water like color) must have a color index of 20-25. Problem analysis Munters studied the existing system; the slippage of LAB in the recovery column was found to be more than 15% and the Acid Color Index was 30-35, sometimes even reaching 60. It was concluded that: - The existing pall rings had performance limitations - The existing distributor and redistributors were found to be inadequate for proper distribution quality Solution provided: The LAB plant was hydraulically rated using Medal-Pak and high-performance distributors. The LAB slippage was found to be within 5-7%. Recommendations to the customer: - Replacement of existing Pall Ring with high-performance Medal-Pak tower packings - Replacement to high-performance distributors and re-distributors to improve distribution quality The tower internals and tower packings were manufactured, supplied and installed accordingly. Results achieved Plant capacity was increased by 20%. LAB slippage was reduced to less than 5% and the ACI also improved to the desired level.
Quick facts
- Customer: Petrochemical industry
- Location: Western India
- Tower Name: Paraffin recovery unit
- Tower Diameter: 1200 mm to 4500 mm
- Mass Transfer Equipment: Random packing (Medal-Pak) and tower internals
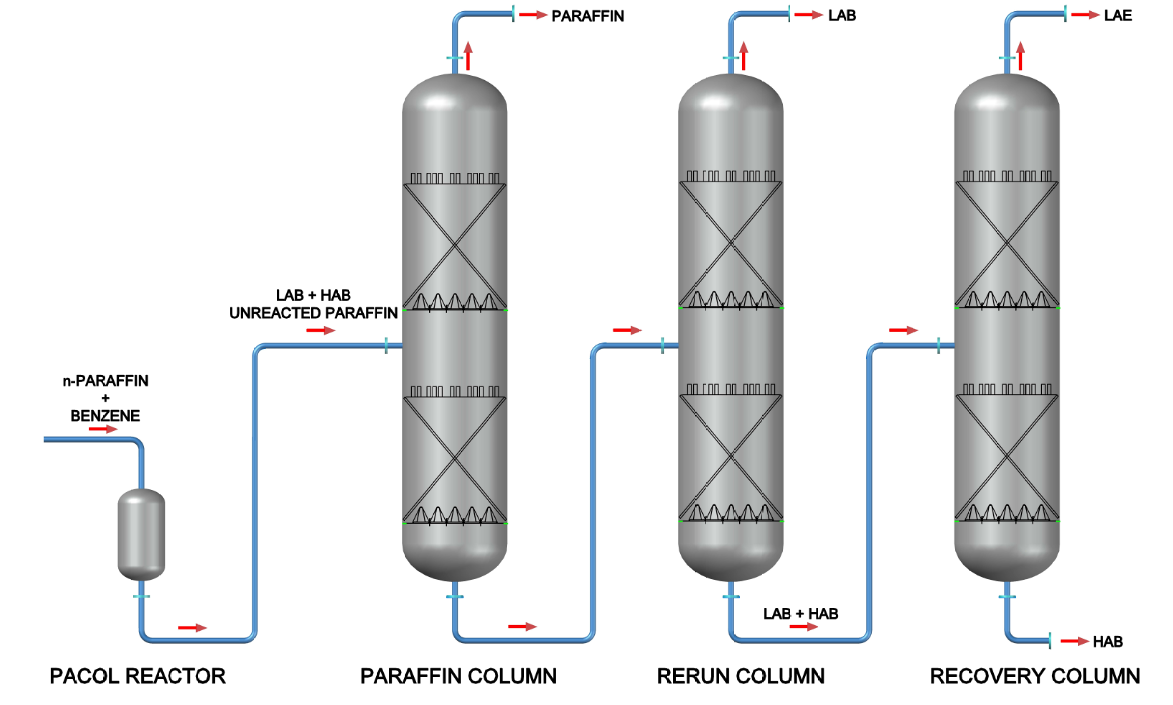
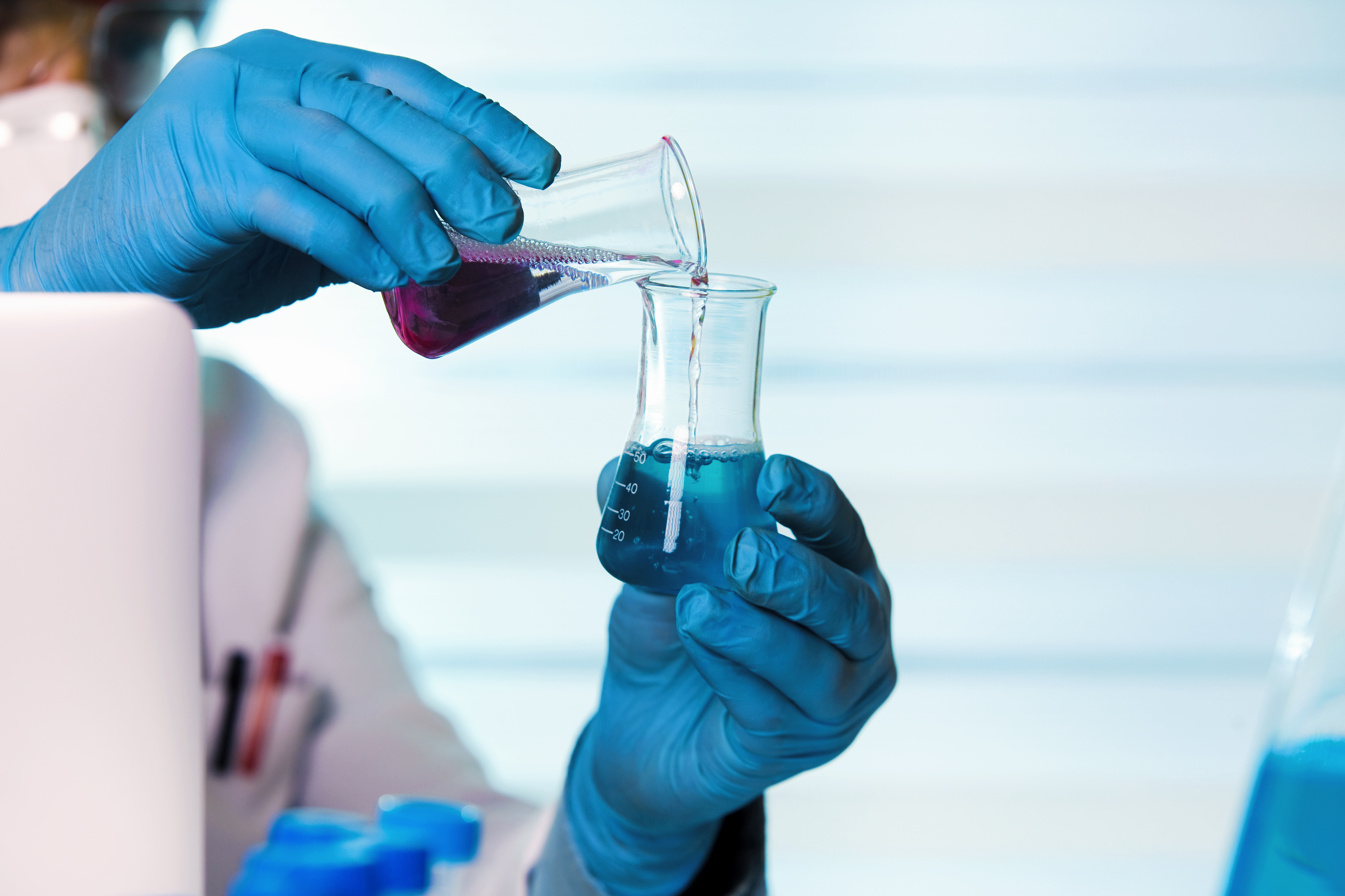