WMG’s Energy Innovation Centre features a battery characterization lab and an electric/hybrid drive testing facility. The Centre features a cutting-edge £13m battery material scale-up pilot program. It´s a one-stop-shop for new battery development, and detailed industrial evaluation of target applications such as, automotive, power grids and consumer electronic products.
Rychlá fakta
- Consistent and accurate conditions
- Turnkey supply of complete dry room
- Achieves an ultra-low dewpoint of -45°C
- Cutting-edge design
- User-friendly monitoring and control
- Energy-efficient
Munters is needed
A specialized Munters air treatment team designed, supplied and installed an energy-efficient dry room featuring the Munters high efficiency MDU system with innovative heat recovery design at its core. A constant -45°C dewpoint provides a stable environment, which is critical. This keeps the electrolytes as dry as possible while producing and testing lithium pouch cells. Any moisture ingress at electrolyte filling can be detrimental to battery performance. The 9m x 5m dry room is just one part of the pilot line, accommodating up to six people, with a relative humidity of less than 1% and a continuous dewpoint of -45°C.
Munters MDU2000
The dry room contains all the pouch cell-making equipment. This is where moisture sensitivity on cell material becomes an issue after electrode drying: Conditions are maintained using the Munters MDU system located next to the dry room. All moisture levels are monitored from here using an integrated Siemens control system. Munters MDU2000 with a built-in high efficiency energy recovery design has a desiccant wheel at the heart of the air treatment system. Munters specialist heat recovery coil design reclaims around 100KW of heat while the unit is running, channeling this to post heating of the dry room, and removing the need for an electric heater of equal size. Staff enter and exit the dry room via an exit through an airlock. Once inside, the air flow is maintained with a laminar flow of 25,000m³/h, moving from a supply wall at one end of the room to an extract wall at the other end. Input from Paul Blackmore, WMG Project Manager “I want to know what moisture my products see at any point of production so I always put the control sensors in the return air side since I know it’s the worst-case scenario.” With a single supplier for all the components of the drying chamber, WMG could begin construction very quickly. Munters took over all details including cabling, lighting, flooring, windows and connections, completing the entire installation within the confines of a demanding deadline. Munters also incorporated energy-efficient LED ceiling lights and static dissipate flooring into the design for added energy-efficiency and practical static control. Extensive service and maintenance options are also available. Paul Blackmore knew he needed to find a supplier to fit the demanding needs of a low dewpoint desiccant wheel system with a proven track record in the battery industry for their state-of-the-art dry room. A successful partnership “I selected Munters due to their historical experience in providing low dewpoint solutions within battery applications.” Munters partnership approach gave us a product that not only was within budget, but also online very quickly. The team also coped well working within a confined space,” said Paul. Munters is dedicated to improving low dewpoint solutions in the lithium battery manufacturing and research industry. Their continuous development of desiccant wheel (rotor) materials and in-house air circulation tools offer low energy consumption while meeting the highest requirements of battery manufacture. The Energy Innovation Centre will be the training ground for the next generation of battery chemists and one of Europe’s leading centers of lithium battery testing.
Rychlá fakta
- Consistent and accurate conditions
- Turnkey supply of complete dry room
- Achieves an ultra-low dewpoint of -45°C
- Cutting-edge design
- User-friendly monitoring and control
- Energy-efficient
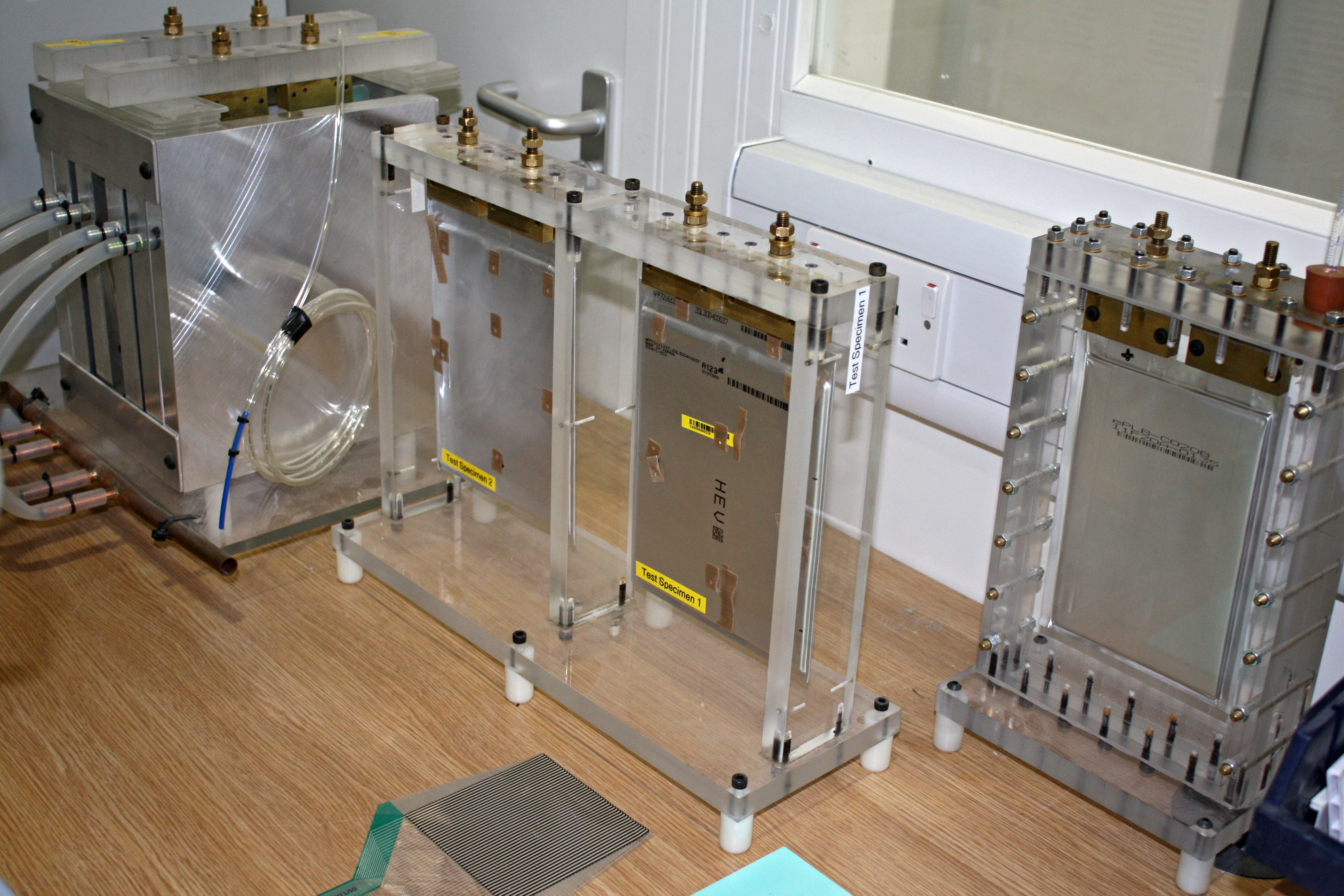
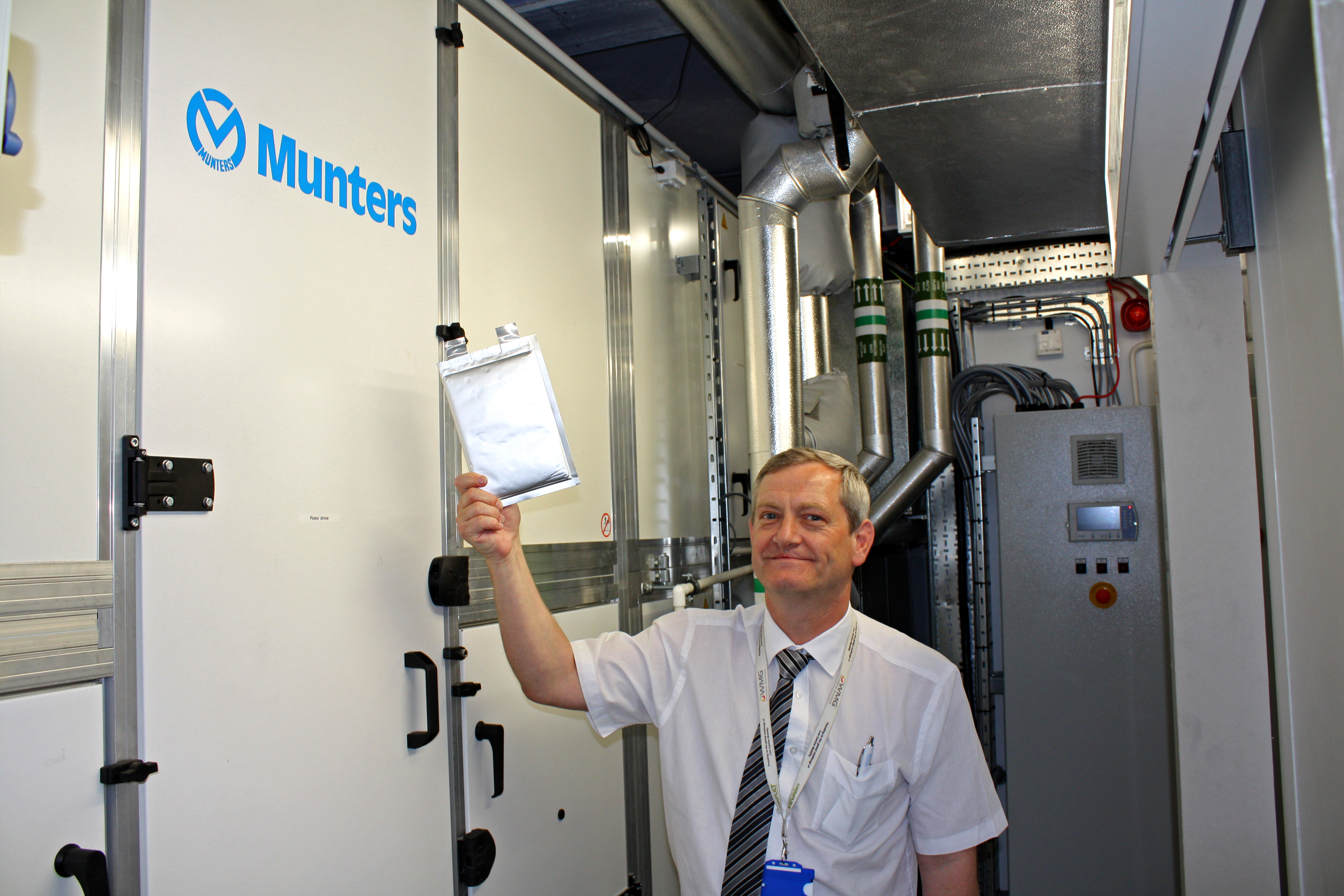
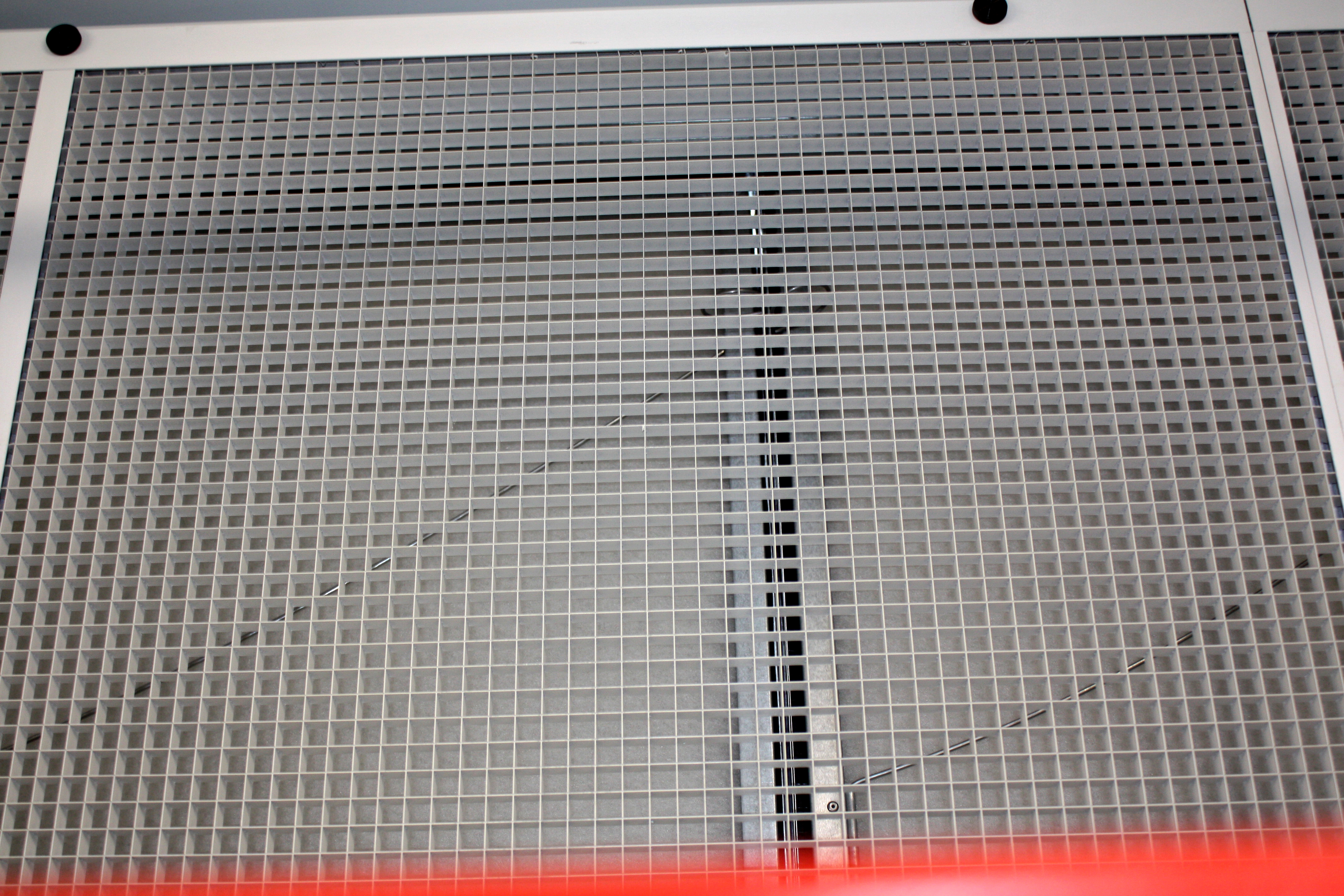
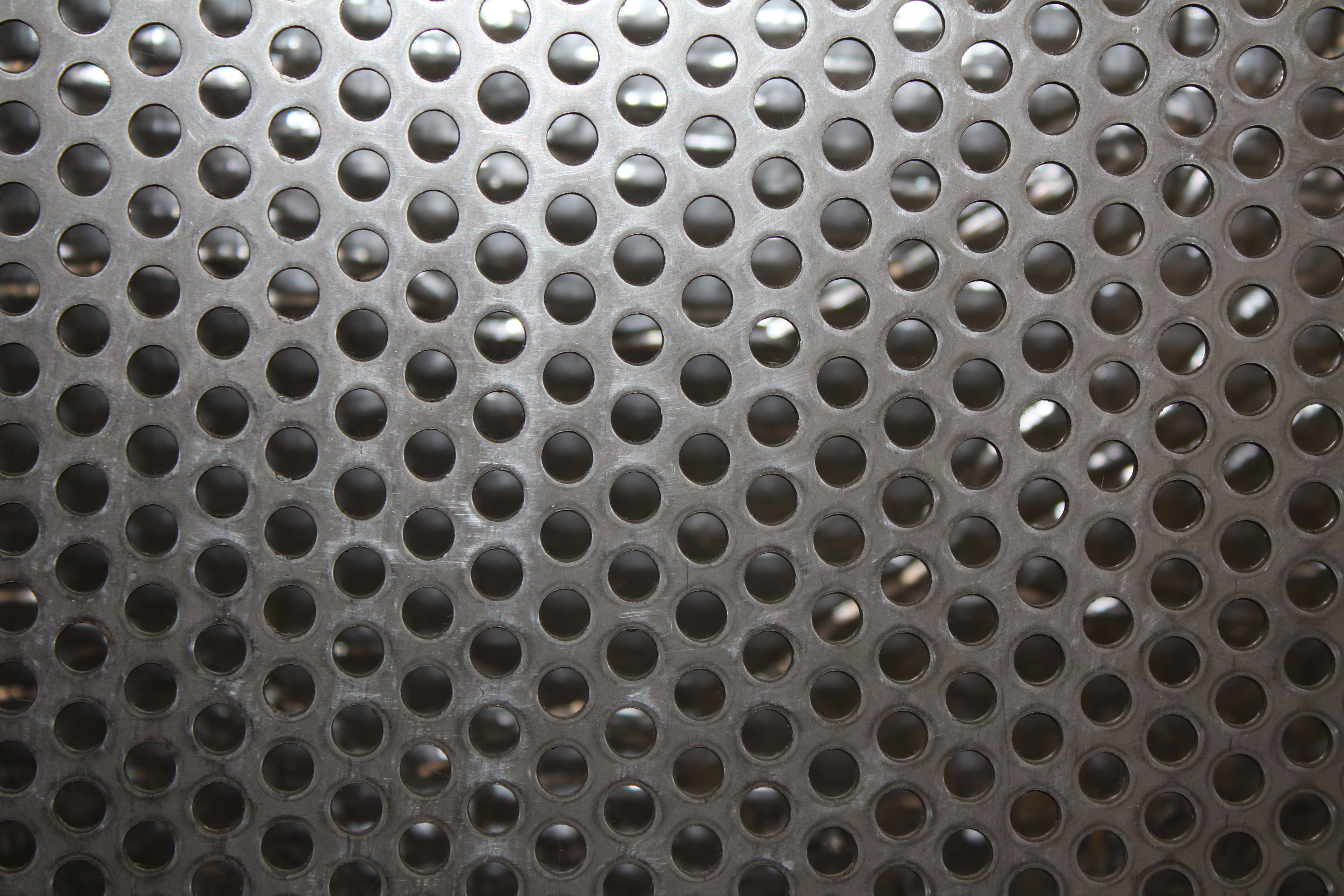
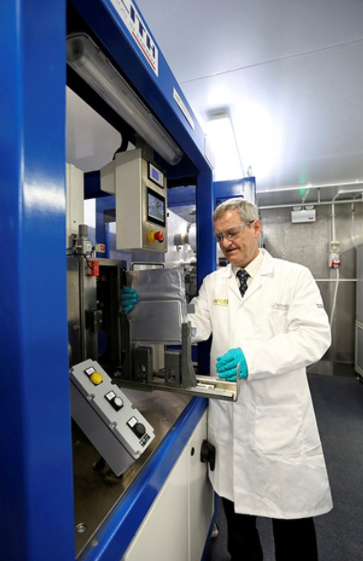